A universal crusher, also known as a crusher machine or mineral crusher, is a highly versatile piece of equipment designed to reduce the size of various minerals. These crushers are crucial in mining, aggregate production, and mineral processing industries, where the primary goal is to break down large rocks, ores, and minerals into smaller, more manageable pieces. Its versatility, efficiency, and robust design make it ideal for crushing different types of minerals, ensuring optimal particle size reduction for further processing.
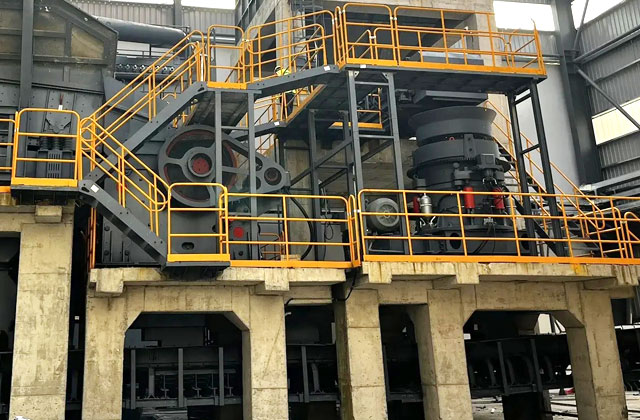
Types of Universal Crushers
- Jaw Crushers: These are the most common type of universal crushers. They use a pair of jaws to crush materials, one fixed and the other moving back and forth. Jaw crushers are particularly effective for primary crushing of large, hard materials such as granite, basalt, and iron ore. The simplicity of design and rugged construction make them reliable and efficient for high-volume production.
- Impact Crushers: These crushers use high-speed impact force to break materials. They are ideal for secondary crushing and fine crushing of materials like limestone, gypsum, and dolomite. Impact crushers can produce more uniform-sized particles, which is beneficial for subsequent processing steps.
- Cone Crushers: Utilizing a rotating cone within a stationary bowl, cone crushers are suitable for crushing medium to hard materials. They provide a high reduction ratio and produce a more cubical product compared to jaw crushers. Cone crushers are commonly used for secondary, tertiary, and quaternary crushing stages.
Types of Minerals Processed
Universal crushers are capable of processing a wide array of minerals, including:
- Hard Rocks and Ores: These include granite, basalt, and iron ore. The high compressive strength and abrasive nature of these materials require a crusher that can withstand significant wear and tear while delivering high crushing efficiency.
- Soft Rocks and Aggregates: These include limestone, dolomite, and gypsum. These materials are easier to crush, and the universal crusher can handle them efficiently without excessive wear.
- Industrial Minerals: Minerals such as talc, graphite, and mica require precise crushing to achieve the desired particle size for further processing. Universal crushers are adaptable to these requirements, ensuring uniformity in particle size distribution.
- Recycled Materials: In the context of sustainability and resource conservation, universal crushers are used to crush construction and demolition waste, such as concrete and asphalt, facilitating recycling and reuse.
Advantages
Versatility
The primary advantage of a universal crusher is its versatility. It can be used in various stages of mineral processing, from primary crushing to secondary and tertiary crushing. This adaptability reduces the need for multiple machines, lowering capital and operational costs.
Durability
Universal crushers are built to handle the toughest materials, with robust construction and wear-resistant components. This durability ensures a long service life, even in demanding mining environments.
Efficiency
With adjustable settings, universal crushers can achieve optimal crushing efficiency for different types of minerals. Operators can fine-tune the machine to ensure the desired particle size and shape, improving downstream processing and overall productivity.
Ease of Maintenance
Modern universal crushers are designed with ease of maintenance in mind. Key components are easily accessible, allowing for quick repairs and minimal downtime. This feature is crucial in maintaining continuous operations and reducing maintenance costs.
Selection and Maintenance
Selecting the appropriate universal crusher depends on factors such as material hardness, desired output size, and production capacity. Key considerations include:
- Material Properties: Hardness, abrasiveness, and moisture content of the material to be crushed.
- Production Requirements: Desired capacity and output size specifications.
- Operational Conditions: Environmental factors, including temperature and humidity.
Proper maintenance is crucial to ensure the longevity and efficiency of universal crushers. Regular inspections, lubrication, and replacement of wear parts are essential practices. Additionally, ensuring that the crusher is operated within its designed parameters can prevent premature wear and damage.
Universal crushers are an essential part of the mineral processing industry, providing a versatile and efficient means of reducing material size for various applications. Their ability to handle a wide range of materials, coupled with their robust construction and efficiency, makes them a valuable investment for any operation involved in mineral processing and aggregate production. With proper selection and maintenance, universal crushers can offer reliable performance and long service life, contributing to the overall success of mining and processing operations.