In the realm of industrial processes where efficiency is paramount, the evolution of screening technology has been instrumental in enhancing productivity and quality control. Among the innovative solutions, the high frequency vibrating screen stands out as a game-changer, offering unparalleled performance in material separation and classification. From mining to aggregate production, its versatility and effectiveness have made it a sought-after equipment across various sectors.
Understanding High Frequency Vibrating Screens
High frequency vibrating screens operate at a rapid speed, typically between 1800-7200 RPM, facilitating the separation of fine particles from a feed mixture. Unlike conventional screens, which rely on gravity and mechanical vibrations, these screens utilize high frequency oscillations to accelerate the separation process. This unique approach allows for finer particle separation, even in cases where conventional screens struggle.
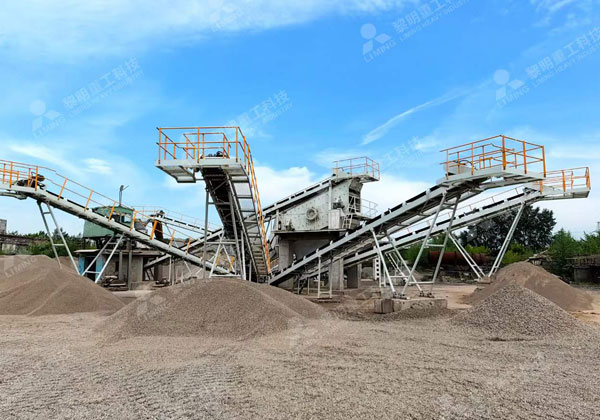
Key Components and Working Principle
A high frequency vibrating screen comprises several essential components, including the screen deck, exciter, and supporting structure. The screen deck consists of multiple layers of mesh or perforated plates, which facilitate the separation process based on particle size. The exciter, usually a motor with eccentric weights, generates high frequency vibrations, imparting energy to the screen deck.
The working principle revolves around the exciter inducing high-frequency vibrations, which cause the particles to stratify based on size and density. Fine particles tend to migrate towards the screen surface, while larger particles remain closer to the feed end. This stratification enables efficient separation, with finer particles passing through the screen apertures, while coarser particles are discharged at the feed end.
Advantages of High Frequency Vibrating Screens
- Enhanced Screening Efficiency: High frequency vibrations enable the screen to process a larger volume of material in a shorter time, increasing overall throughput and productivity.
- Improved Particle Separation: The rapid oscillations prevent particles from blinding the screen apertures, ensuring accurate separation of fine and coarse materials.
- Higher Accuracy: Fine particle separation is achieved with precision, leading to better product quality and consistency.
- Versatility: High frequency vibrating screens are adaptable to various applications, including wet and dry screening, making them suitable for diverse industries such as mining, construction, and recycling.
- Reduced Maintenance: Compared to traditional screens, high frequency vibrating screens experience lower wear and tear due to reduced mechanical stress, resulting in longer service life and reduced downtime.
- Space Efficiency: Compact design and high screening capacity make these screens ideal for installations where space is limited, optimizing plant layout and operational efficiency.
- Energy Efficiency: The efficient screening process consumes less energy per ton of material processed, contributing to cost savings and sustainability.
Applications Across Industries
High frequency vibrating screens find applications across a wide range of industries:
- Mining: Used for ore classification, dewatering, and processing of fine particles.
- Aggregate: Effective in separating sand, gravel, and crushed stone for concrete production and road construction.
In the realm of material processing, the high frequency vibrating screen stands as a testament to innovation and efficiency. Its ability to deliver precise particle separation, coupled with its versatility and low maintenance requirements, has cemented its position as a vital asset across numerous industries. As industrial processes continue to evolve, the high frequency vibrating screen remains at the forefront, revolutionizing screening efficiency and setting new standards for performance and reliability.