VSI6X series sand making machine is also called vertical shaft impact crusher. It is a kind of impact crusher with high level of high energy and low consumption. Its performance plays an irreplaceable role in various ore fine crushing equipment. Reliable sand making equipment is widely used in glass raw materials, building aggregates, artificial sand making, and fine crushing and coarse grinding of various metallurgical slag.
Production capacity: 12-650t/h
Feed particle size: ≤60mm
Applicable materials: pebbles, river pebbles, river stones, granite, iron ore, calcite, quartz stone, etc.
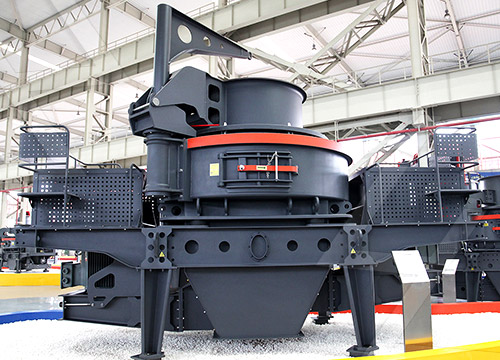
Performance advantages of vSI6X series sand making machine
(1) High output and low energy consumption: the sand making machine has a shaping function, the product is cubic, and the bulk density is large; the output is high, and the energy consumption is 20% less than other sand making machines, and the crushing ratio is large.
(2) The design is compact and reasonable: the structure is novel, the operation is stable, and the downtime can be reduced by 30%; the equipment is small in size, easy to operate, easy to install and maintain.
(3) The wear-resistant life of the body is long: in the production process, the stone material can form a protective bottom layer, the body wears less and is durable; a small number of wear-resistant parts are made of extra-hard wear-resistant materials, which are small in size, light in weight, and easy to replace accessories .
(4) Matching with mobile crushing station: The mobile sand making machine is equipped with an intelligent operating system, which has high operating efficiency; flexible configuration, no need for piling, and more free transitions, which can save customers a lot of manpower and infrastructure costs during operation.
working principle of VSI6X series sand making machine
The material falls into the high-speed rotating turbine crushing cavity from the top of the machine. Under the action of centrifugal force, the high-speed rotating impeller and another part of the material shunted around the impeller in the form of an umbrella generate high-speed collision and crushing. After the materials collide with each other, they will be crushed again. A vortex is formed between the impeller and the casing, and the material layer is smashed by repeated impact and friction, and discharged from the lower discharge hopper. A closed circuit is formed for multiple cycles, and the particle size of the finished product is controlled by the screening equipment.
Specifications – Technical Data