A manganese crushing and screening plant plays a crucial role in processing manganese ore into various usable forms. Manganese is a chemical element with symbol Mn and atomic number 25. It is widely used in various industrial sectors, including metallurgy, mining, and manufacturing of different types of products.
Introduction to Manganese:
Manganese is an essential metal in modern industry, primarily used in the production of steel. It enhances the strength, toughness, and hardenability of steel, making it an indispensable component in construction, transportation, and infrastructure projects. Apart from its metallurgical applications, manganese compounds find uses in batteries, ceramics, pigments, and fertilizers, among other things.
The Importance of Crushing and Screening Plants:
The process of extracting manganese ore from the ground involves several stages, including crushing, screening, and beneficiation. Crushing and screening are fundamental processes that significantly impact the efficiency and cost-effectiveness of manganese processing operations. A well-designed crushing and screening plant is critical for optimizing the production of high-quality manganese products.
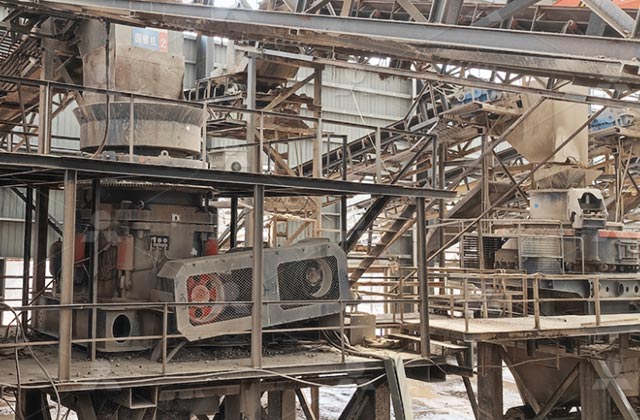
Crushing Stage:
The crushing stage involves breaking down the manganese ore into smaller pieces of a manageable size. This is typically achieved using various types of crushers, such as jaw crushers, cone crushers, or impact crushers. The choice of crusher depends on factors such as the hardness of the ore, the desired product size, and the production capacity required.
Jaw crushers are commonly used for primary crushing, as they can handle large rocks and produce a uniform product size. Cone crushers are suitable for secondary and tertiary crushing, providing finer particle sizes and better shape for the final product. Impact crushers are often used for shaping purposes and can produce cubic-shaped particles.
Screening Stage:
After crushing, the manganese ore undergoes screening to separate the material into different sizes or grades. Screening is essential for removing unwanted fines and ensuring that the ore meets the specifications required for further processing. Vibrating screens are commonly used in manganese screening plants, where the ore is sorted into various size fractions.
Beneficiation Process:
Once the ore has been crushed and screened, it undergoes a beneficiation process to remove impurities and improve its quality. Common beneficiation techniques include gravity separation, magnetic separation, and flotation. These processes help increase the manganese content of the ore and reduce the levels of contaminants, resulting in a higher-grade product.
Plant Design and Optimization:
The design of a manganese crushing and screening plant depends on various factors, including the type of ore, the desired product specifications, the production capacity, and the overall layout of the facility. A well-designed plant incorporates efficient equipment selection, optimized process flows, and robust control systems to ensure smooth operation and maximum productivity.
Regular maintenance and monitoring are essential for optimizing the performance of a crushing and screening plant. This includes routine inspections, lubrication of moving parts, and timely replacement of worn-out components. Additionally, process optimization techniques, such as adjusting crusher settings and fine-tuning screening parameters, can help improve efficiency and reduce operating costs.
In conclusion, a manganese crushing and screening plant is a vital component of manganese processing operations, playing a crucial role in producing high-quality manganese products for various industrial applications. By incorporating efficient equipment, optimized processes, and environmental management practices, manganese producers can enhance productivity, reduce costs, and minimize their environmental footprint.