A secondary crusher plays a crucial role in a rock crushing plant. This type of crusher is responsible for further breaking down the material that is delivered from the primary crusher, ensuring that it reaches the desired size for the production of aggregates or other end products. The selection of an appropriate secondary crusher is critical for the overall efficiency and success of the crushing process.
One commonly used type of secondary crusher is the cone crusher. Cone crushers are versatile machines that excel in secondary and tertiary crushing applications. They operate by squeezing the material between an eccentrically gyrating spindle and a concave hopper, which is covered by a manganese concave or a bowl liner. The material is crushed and falls out of the bottom.
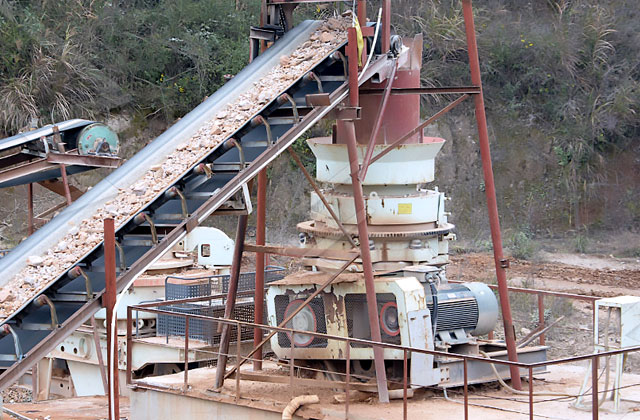
Another popular choice for secondary crushing is the impact crusher. Impact crushers use the principle of rapid impact to break rocks. The material is fed into a chamber, where it is accelerated and then struck by hammers or blow bars. This impact causes the material to break along its natural cleavage planes.
Each type of secondary crusher has its advantages and is suitable for different types of rocks and applications. The choice between cone crushers and impact crushers depends on factors such as the hardness of the rock, the desired end product size, and the production requirements. Some rocks are better suited for compression crushing with cone crushers, while others may be more suitable for impact crushing.
In addition to cone crushers and impact crushers, there are also other types of secondary crushers, such as gyratory crushers and jaw crushers. Gyratory crushers operate on the same principle as cone crushers but have a different shape of crushing chamber. Jaw crushers, on the other hand, compress the material between two jaws, one stationary and one movable.
The secondary crusher in a rock crushing plant is a critical component because it directly influences the efficiency of the entire crushing process. It must be selected carefully to ensure that it is capable of handling the specific characteristics of the material being processed. Factors such as feed size, hardness, and abrasiveness of the rock, as well as the required end product size, should all be considered during the selection process.
The secondary crusher not only impacts the crushing process but also affects the overall plant design. The type and size of the secondary crusher may influence the layout of the plant, the conveyor systems, and the location of the screening equipment. Proper integration of the secondary crusher into the overall plant design is essential to ensure a smooth and efficient operation.
Regular maintenance and inspections are crucial to ensure the reliable performance of the secondary crusher. This includes checking wear parts, such as the concave liners in cone crushers or the blow bars in impact crushers, and replacing them when necessary. Proper maintenance practices contribute to the longevity of the equipment and help prevent unplanned downtime.
The secondary crusher in a rock crushing plant is a vital component that plays a key role in the production of high-quality aggregates. The choice of the secondary crusher depends on various factors, including the type of rock, production requirements, and end product specifications. Careful consideration and proper maintenance are essential to ensure the efficient and reliable operation of the secondary crushing process.