A gyratory crusher is a type of primary crusher used in ore processing plants. Its key function is to reduce large pieces of rock into smaller particles for subsequent crushing stages. Gyratory crushers have a conical head and concave surface, often lined with manganese steel, and break apart material by compression through an eccentrically gyrating spindle. Understanding the equipment operation of a gyratory crusher is crucial for efficient and safe operation in mining and mineral processing operations.
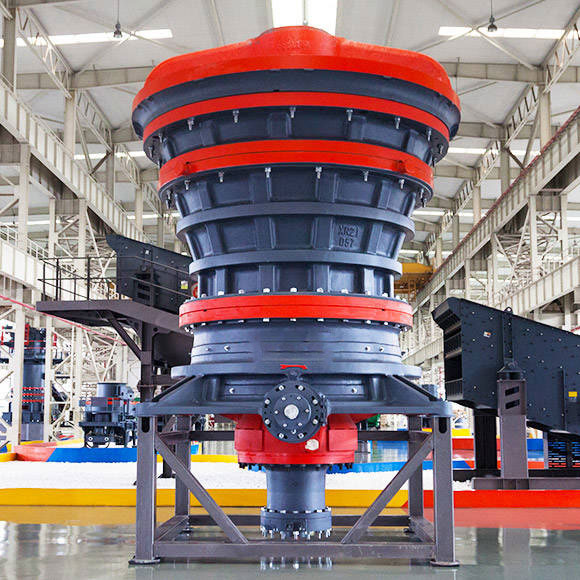
- Start-Up Procedure:
- Prior to starting the gyratory crusher, operators must conduct a pre-operational inspection to ensure all components are in good condition.
- Check for any loose or damaged parts that may affect operation or safety.
- Verify that the lubrication system is filled and operational.
- Ensure proper power supply and safety protocols are in place.
- Loading Material:
- Material should be evenly distributed across the entire width of the crusher’s inlet to prevent uneven wear and optimize crushing efficiency.
- Excessive bridging or blockages should be cleared before operation to prevent damage to the crusher.
- Operators must adhere to maximum feed size guidelines to prevent overloading the crusher and causing potential damage.
- Adjusting Settings:
- Gyratory crushers typically offer variable settings for controlling the crusher’s output size.
- Operators can adjust the eccentricity (eccentric throw) to control the size of the crushed product.
- Additionally, the crusher’s CSS (closed side setting) can be adjusted to regulate the product size distribution.
- Proper adjustment of settings ensures optimal performance and product quality.
- Monitoring Operation:
- Operators must continuously monitor the crusher’s operation for any signs of abnormalities or potential issues.
- Watch for excessive vibration, unusual noises, or fluctuations in operating parameters.
- Regularly check the oil temperature, pressure, and flow rate to ensure proper lubrication and cooling.
- Keep an eye on the crusher’s power consumption and throughput to assess its performance.
- Maintenance:
- Regular maintenance is essential for ensuring the longevity and reliability of a gyratory crusher.
- Conduct routine inspections of key components such as the spider bushing, mantle, and concaves for signs of wear or damage.
- Replace worn-out parts promptly to prevent further damage to the crusher and maintain optimal performance.
- Lubricate moving parts as per the manufacturer’s recommendations to reduce friction and wear.
- Shutdown Procedure:
- Before shutting down the gyratory crusher, operators should clear the crushing chamber of any remaining material.
- Turn off the power supply and follow proper lockout/tagout procedures to prevent accidental startup.
- Conduct post-operational inspections to identify any maintenance or repair requirements.
- Document any issues or abnormalities encountered during operation for future reference.
- Safety Considerations:
- Operators must adhere to all safety protocols and regulations while operating a gyratory crusher.
- Wear appropriate personal protective equipment (PPE), including safety glasses, hard hats, and hearing protection.
- Never perform maintenance or repairs on the crusher while it is in operation.
- Follow established procedures for working at heights and confined spaces when accessing crusher components.
- Provide proper training for personnel involved in operating and maintaining gyratory crushers to mitigate the risk of accidents or injuries.
In conclusion, efficient and safe operation of a gyratory crusher requires careful attention to detail, adherence to proper procedures, and regular maintenance. By following best practices and prioritizing safety, operators can maximize the productivity and longevity of their equipment while minimizing the risk of downtime or accidents.