Non-metallic ore extraction involves the process of obtaining valuable minerals or rocks from deposits that do not contain metallic elements. The primary crusher plays a crucial role in this extraction process by reducing the size of the ore into smaller, more manageable pieces. In this article, we will explore the significance of the primary crusher in non-metallic ore extraction and discuss its key functions and operational aspects.
The primary crusher is the initial stage of the ore processing chain and is responsible for reducing the ore size to a level suitable for further processing. It is typically the first piece of equipment encountered in the extraction process and often located near the mining site. The primary crusher operates by exerting mechanical force on the ore, breaking it into smaller fragments. This reduction in size enhances the efficiency of subsequent processing steps.
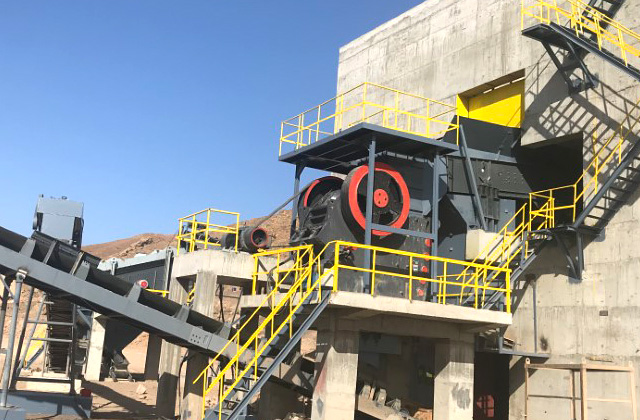
One of the primary functions of the primary crusher is to facilitate efficient transportation and handling of the ore. The ore extracted from the mining site is often bulky and uneven in size. By reducing the ore size, the primary crusher enables easier loading onto trucks or conveyors for transportation to the processing plant. Smaller ore fragments are also more manageable during subsequent processing stages, such as grinding and sorting.
Another important function of the primary crusher is to maximize the liberation of valuable minerals from the ore matrix. Non-metallic ores can contain valuable minerals such as phosphate, limestone, gypsum, or quartz, among others. These minerals are often embedded within the ore and need to be liberated before they can be separated and processed further. The primary crusher breaks down the ore, exposing the valuable minerals and making them accessible for subsequent extraction processes.
Efficiency and throughput are critical considerations for the primary crusher. The crusher must be capable of handling large volumes of ore while maintaining a consistent and reliable performance. The design of the primary crusher takes into account factors such as the hardness and abrasiveness of the ore, as well as the desired final product size. Various types of crushers, including jaw crushers, gyratory crushers, and impact crushers, can be used as primary crushers depending on the specific requirements of the ore and the processing plant.
To ensure smooth and efficient operation, the primary crusher requires regular maintenance and monitoring. This includes routine inspections, lubrication, and replacement of worn-out components. Timely maintenance helps prevent unexpected breakdowns and extends the lifespan of the equipment, minimizing downtime and maximizing productivity.
In conclusion, the primary crusher is a crucial component in the non-metallic ore extraction process. It reduces the size of the ore, facilitates transportation, and enhances the liberation of valuable minerals. The primary crusher plays a vital role in optimizing the efficiency and productivity of the extraction operation. By understanding its functions and implementing proper maintenance practices, mining operations can ensure the smooth operation of the primary crusher and achieve optimal results in non-metallic ore extraction.