A gravel crusher is a machine designed to reduce large rocks into smaller rocks, gravel, or rock dust. It plays a crucial role in various construction and mining applications, providing the necessary material for building roads, foundations, and other infrastructure projects. Setting up and operating a gravel crusher requires careful consideration of the equipment needed to achieve optimal efficiency and productivity. In this essay, we will explore the essential equipment required for a gravel crusher operation.
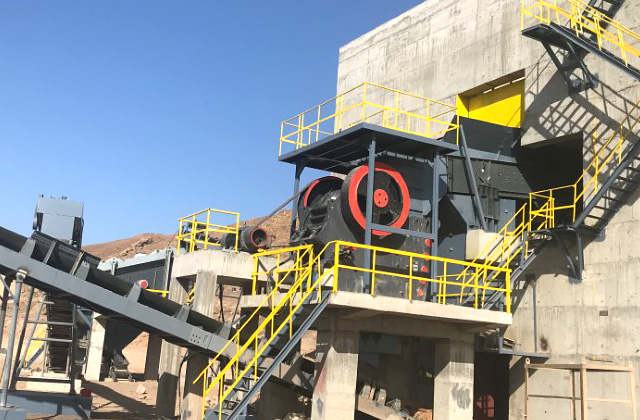
Primary Crusher:
The primary crusher is the initial machine used to break down large rocks into smaller pieces. Common types include jaw crushers, gyratory crushers, and impact crushers. The choice of the primary crusher depends on factors such as the hardness and size of the material. Jaw crushers are popular for their simplicity and reliability, while impact crushers are effective for producing cubic-shaped aggregates.
Feeder:
A feeder is essential to regulate the flow of material into the crusher. It ensures a steady and controlled supply of rocks, preventing overloading and optimizing the crusher’s performance. Vibrating grizzly feeders are commonly used in gravel crushing operations to remove fines and improve efficiency.
Conveyor System:
Conveyors are critical for transporting material between different stages of the crushing process. They help maintain a continuous flow of material, reducing downtime and increasing overall efficiency. Conveyors can be used to transport material from the primary crusher to secondary crushers, screening units, or stockpiles.
Secondary Crushers:
Secondary crushers are used to further reduce the size of the crushed material. Common types include cone crushers and impact crushers. The secondary crusher helps produce finer and more consistent gravel sizes.
Screening Equipment:
After crushing, screening equipment is used to separate the different sizes of gravel. This is crucial for producing high-quality aggregates with uniform particle sizes. Vibrating screens or deck screens are commonly employed in gravel crushing plants for efficient screening.
Washing Equipment:
Washing equipment is used to remove impurities and fines from the crushed gravel, producing cleaner and more marketable products. This is particularly important for applications such as concrete production. Sand screws or cyclones are commonly used in gravel washing operations.
Stockpiling and Storage:
Adequate space for stockpiling and storage of various gravel products is essential. This ensures a continuous supply of material for construction projects and allows for efficient management of inventory.
Dust Suppression System:
Gravel crushing operations can generate dust, which poses health and environmental risks. A dust suppression system, such as water sprays or misting systems, helps control airborne particles, improving air quality and creating a safer working environment.
Power Source:
A reliable and sufficient power source is critical for operating the entire gravel crushing plant. Depending on the scale of the operation, this may involve connecting to the local power grid or using generators.
Maintenance Tools and Equipment:
Regular maintenance is crucial to ensure the longevity and efficiency of the equipment. Adequate tools, lubricants, and spare parts should be readily available to address routine maintenance and promptly address any issues that may arise.
Setting up a gravel crusher requires a well-thought-out selection of equipment to ensure efficient and productive operations. Each component plays a vital role in the crushing process, from the primary crusher that initiates the process to the screening and washing equipment that refines the final product. Regular maintenance and proper management of the overall system contribute to the long-term success of gravel crushing operations.