A hammer crusher is a machine used to shred or crush materials into smaller pieces. It operates on the basic principle of impact crushing, where the hammerhead rotates at high speed and strikes the material in the crushing chamber. The material is then crushed or shattered upon impact. The working capacity of a hammer crusher depends on various factors, including the type of material being crushed, the size and shape of the hammers, the rotor speed, the screen size, and the design of the crushing chamber.
The primary components of a hammer crusher include the rotor, hammers, and the crushing chamber. The rotor is the main rotating component, and it is typically driven by an electric motor or a diesel engine. The hammers are attached to the rotor and swing outward when the rotor rotates. The crushing chamber, usually enclosed by a grate or a screen, contains the material to be crushed.
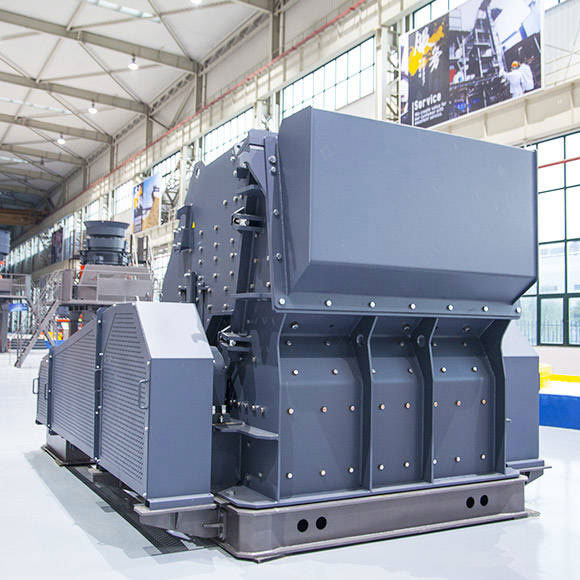
The working capacity of a hammer crusher is influenced by the following factors:
- Material Characteristics: The type of material being crushed is a crucial factor. Different materials have varying hardness, abrasiveness, and friability. Harder and more abrasive materials require more robust hammers and higher impact energy.
- Hammer Design: The design of the hammers is essential for efficient crushing. The shape, weight, and distribution of the hammers impact their ability to break the material. Heavy, well-designed hammers can crush tough materials effectively.
- Rotor Speed: The speed at which the rotor rotates affects the impact force and the crushing capacity. Higher rotor speeds generally result in higher impact energy, but there is a limit beyond which increasing the speed may not significantly improve performance.
- Screen Size: The size of the openings in the screen or grate at the bottom of the crushing chamber determines the final product size. Smaller screen openings produce finer materials, but they may reduce the overall throughput.
- Feed Rate: The rate at which material is fed into the crusher also affects its working capacity. Too high a feed rate may lead to overloading, while too low a feed rate may result in underutilization of the crusher’s capacity.
- Crushing Chamber Design: The design of the crushing chamber influences the trajectory of the material and the impact force. An optimized chamber design ensures efficient crushing.
- Maintenance and Wear: Regular maintenance, including the replacement of worn-out hammers and other components, is essential for sustained performance.
The working capacity of a hammer crusher is a complex interplay of various factors. Proper consideration of material properties, hammer design, rotor speed, screen size, feed rate, and maintenance is crucial for optimizing the crusher’s performance and achieving the desired crushing outcomes. It is important for operators to understand these factors and adjust the crusher parameters accordingly to ensure efficient and reliable operation.