A bauxite processing plant is a facility that is used to extract and refine valuable metals from raw bauxite ore, the primary source of aluminum. Bauxite, a reddish-brown rock composed of aluminum oxide and other minerals, is a crucial ingredient in the production of aluminum. The processing plant plays a pivotal role in transforming bauxite into alumina, the intermediate product that serves as the feedstock for aluminum smelting. In this essay, we will explore the key components and processes involved in a typical bauxite processing plant, with a focus on the crusher, a fundamental unit responsible for breaking down the raw material.
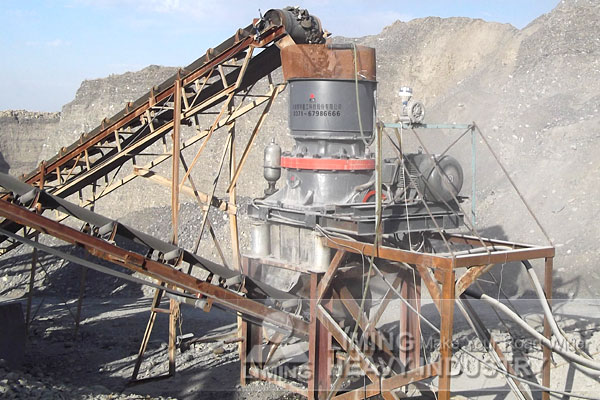
Mining and Transportation: The first step in the bauxite processing chain is mining. Large-scale open-pit mining operations are commonly employed to extract bauxite deposits located near the Earth’s surface. Once mined, the bauxite ore is transported to the processing plant via trucks, conveyors, or railways. This transportation phase is critical to ensuring a steady supply of raw material to the processing facility.
Crushing Process: Upon arrival at the processing plant, the bauxite ore undergoes a series of preparatory steps, with crushing being a primary operation. The crusher is a mechanical machine designed to reduce the size of bauxite ore particles, facilitating subsequent processing stages. Various types of crushers are used in bauxite processing, including jaw crushers, impact crushers, and cone crushers.
Jaw Crushers: Jaw crushers are commonly used in bauxite processing plants for primary crushing. These robust machines consist of a fixed jaw and a movable jaw. The ore is fed into the space between the jaws, and as the jaws compress the material, it is fractured into smaller, manageable pieces. This initial reduction in size is crucial for downstream processes.
Impact Crushers: Impact crushers are another type of crusher used in bauxite processing. They operate by impacting the ore with hammers or blow bars, causing it to break along natural fault lines. Impact crushers are effective for producing angular and fine particles, enhancing the efficiency of subsequent processing steps.
Cone Crushers: Cone crushers are utilized for secondary and tertiary crushing in bauxite processing. These machines have a cone-shaped crushing chamber where the material is crushed between an eccentrically rotating mantle and a concave liner. Cone crushers produce a well-shaped product and are often used for finer crushing requirements.
Screening and Grinding: Following the initial crushing stage, the crushed bauxite undergoes screening to separate finer particles. The oversized material is then returned to the crusher for further processing. The screened material is subjected to grinding, which reduces the particle size further, preparing it for the next phase of the processing chain.
Alumina Extraction: After crushing, the bauxite is subjected to a process called digestion, where it is mixed with a hot caustic soda solution to dissolve the aluminum compounds. This results in the formation of alumina, the primary product of bauxite processing. The remaining solid residue, known as red mud, contains impurities and is separated from the alumina.
Bauxite processing plant is a complex facility where raw bauxite ore is transformed into alumina, a crucial intermediate product for aluminum production. The crusher, as an essential component of the processing chain, plays a vital role in breaking down the raw material to a size suitable for further processing. The efficiency of the crushing process influences the overall performance and productivity of the bauxite processing plant. As technology advances, the industry continues to explore innovative approaches to optimize the processing of bauxite, aiming for increased efficiency, reduced environmental impact, and sustainable production practices.