Secondary crushing in a quarry plays a crucial role in the overall processing of extracted materials. This phase involves breaking down the raw material into smaller, more manageable sizes, preparing it for further processing or final use. The choice of secondary crushing equipment in a quarry is a critical decision that directly impacts the efficiency, cost-effectiveness, and overall productivity of the entire operation.
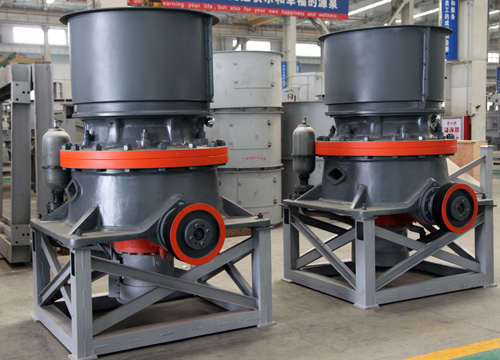
Several types of secondary crushing equipment are commonly used in quarries, each with its own unique characteristics and advantages. These include:
- Impact Crushers:
- Working Principle: Impact crushers involve the use of impact rather than pressure to crush material. They utilize the fast rotational motion of hammers or impellers, which are attached to a rotor.
- Advantages: Impact crushers are versatile and suitable for various materials. They provide high reduction ratios and are effective in producing a uniform cubic product.
- Considerations: Maintenance costs and wear parts replacement should be taken into account when choosing impact crushers.
- Cone Crushers:
- Working Principle: Cone crushers operate on the principle of compression crushing. Material is fed into the crushing chamber, and the crushing head gyrates within it, compressing the material against the stationary concave.
- Advantages: Cone crushers are known for their efficiency in producing well-shaped and finely graded materials. They are also suitable for hard and abrasive materials.
- Considerations: The initial cost, maintenance, and the potential for blockages are factors to consider when selecting cone crushers.
- Jaw Crushers:
- Working Principle: Jaw crushers are designed to handle primary crushing but are often used in secondary crushing applications. They consist of a fixed jaw and a moving jaw that exerts pressure on the material.
- Advantages: Jaw crushers are simple to operate and maintain. They are cost-effective and suitable for a wide range of materials.
- Considerations: Jaw crushers may not be as efficient in producing fine materials compared to cone crushers.
- Gyratory Crushers:
- Working Principle: Gyratory crushers consist of a mantle that gyrates within a concave bowl. Material is fed into the top of the crusher and is crushed between the mantle and concave.
- Advantages: Gyratory crushers are capable of handling large-sized feed and are often chosen for high-capacity applications.
- Considerations: They tend to have higher initial costs and may require more maintenance compared to other types of crushers.
When selecting secondary crushing equipment for a quarry, it’s crucial to consider the type and characteristics of the material being processed, production requirements, energy efficiency, and maintenance costs. Additionally, the integration of the secondary crushing process with the overall plant design is essential for optimizing the entire material processing workflow in a quarry operation. Regular maintenance and monitoring are key aspects of ensuring the continued efficiency and reliability of the chosen secondary crushing equipment in a quarry setting.