High-capacity stone crushers are essential equipment in the mining, construction, and aggregate industries, designed to efficiently crush large quantities of stone. These crushers vary in design and functionality to suit different applications. In this article, we will explore various types of high-capacity stone crushers, highlighting their key features and applications.
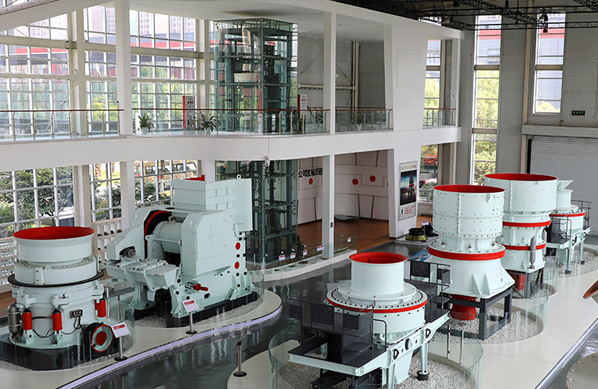
- Jaw Crusher:
- Design: Jaw crushers consist of a fixed jaw and a moving jaw. The moving jaw is mounted on an eccentric shaft, creating an oscillating motion.
- Working Principle: Stone is fed into the crushing chamber and crushed between the jaws, producing a uniform-sized product.
- Advantages: Simple structure, high capacity, versatile for various materials.
- Applications: Primary crushing in quarrying, mining, and recycling.
- Cone Crusher:
- Design: Cone crushers have a conical-shaped crushing chamber and a gyrating spindle with a mantle.
- Working Principle: Stone is fed into the top of the cone crusher and is crushed as it falls between the mantle and the bowl liner.
- Advantages: High capacity, good product shape, suitable for secondary and tertiary crushing.
- Applications: Aggregate production, mining, and secondary/tertiary crushing.
- Impact Crusher:
- Design: Impact crushers utilize impact force to crush stone. They can be either horizontal shaft impactors (HSI) or vertical shaft impactors (VSI).
- Working Principle: Stone is fed into the crusher and impacted by hammers or the centrifugal force of the rotor, producing smaller-sized particles.
- Advantages: Versatility, high reduction ratio, suitable for various types of stone.
- Applications: Primary, secondary, and tertiary crushing in mining and construction.
- Gyratory Crusher:
- Design: Gyratory crushers have a conical head and a concave surface, forming a tapered crushing chamber.
- Working Principle: Stone is fed into the top of the gyratory crusher and is crushed as it gyrates, producing finer-sized particles.
- Advantages: High capacity, continuous operation, ideal for large-sized materials.
- Applications: Primary crushing in mining and large-scale quarry operations.
- Hammer Crusher:
- Design: Hammer crushers have rotating hammers attached to a rotor, crushing stone against the housing.
- Working Principle: Stone is fed into the crusher and impacted by the rotating hammers, producing smaller-sized particles.
- Advantages: Simple structure, high capacity, suitable for soft to medium-hard materials.
- Applications: Primary and secondary crushing in mining and construction.
High-capacity stone crushers come in various types, each designed for specific applications and material characteristics. The choice of crusher depends on factors such as feed size, hardness of the stone, required product size, and desired capacity. Whether it’s primary, secondary, or tertiary crushing, these machines are crucial for efficiently processing large quantities of stone in diverse industries.