A granite crushing plant control system plays a crucial role in optimizing the production process and ensuring efficient operations. The primary goal of such a system is to manage the various components of the crushing plant to achieve high productivity, quality output, and safety. In this article, we will explore the key aspects of a granite crushing plant control system.
One of the fundamental components of the control system is the centralized control room. This room serves as the nerve center where operators monitor and control the entire crushing process. Advanced human-machine interface (HMI) systems provide operators with real-time data, visualizations, and controls to make informed decisions. The HMI displays information about equipment status, production rates, material flow, and other critical parameters.
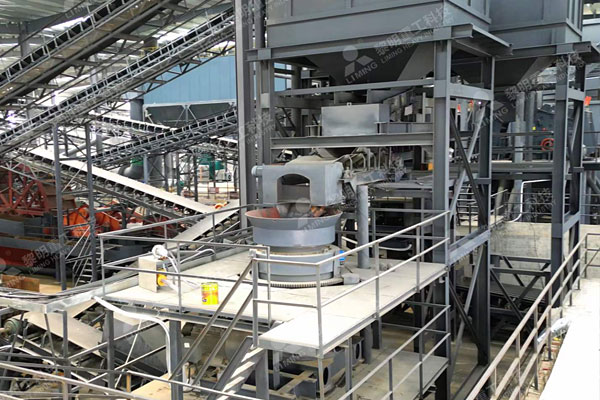
The control system incorporates sensors and instruments strategically placed throughout the crushing plant. These sensors continuously collect data on various parameters such as feed rate, crusher power draw, conveyor belt speed, and particle size distribution. The data from these sensors are transmitted to the central control system, allowing operators to have a comprehensive view of the plant’s performance.
Automation is a key feature of modern granite crushing plant control systems. Automated processes help optimize the plant’s efficiency by adjusting settings in real-time based on the incoming feed, material characteristics, and production goals. For example, automated systems can dynamically adjust the crusher settings to maintain optimal throughput and particle size distribution.
Integrated safety features are critical to protect both personnel and equipment. Emergency stop systems, interlocks, and alarms are implemented to respond quickly to any abnormal conditions. The control system continuously monitors safety parameters and takes immediate actions to mitigate risks, ensuring a safe working environment.
Material tracking is another essential aspect of the control system. RFID tags or other tracking technologies are often used to trace the movement of materials from the quarry to the final product. This tracking capability enables better inventory management, quality control, and ensures that the right material is processed at the right time.
Energy management is increasingly becoming a focus in crushing plant control systems. Advanced systems can optimize energy consumption by adjusting equipment operation based on energy costs, demand, and other factors. This not only reduces operational costs but also contributes to sustainability goals by minimizing the environmental impact.
Maintenance planning and predictive maintenance are integrated into the control system to ensure that equipment operates at peak performance. The system analyzes data from sensors to predict potential issues and schedule maintenance activities proactively. This approach minimizes downtime and extends the lifespan of critical components.