Metal ore impact crushers are essential components in mining and construction industries, designed to break down large rocks and ores into smaller, more manageable pieces. These machines rely on wear parts to effectively crush and process materials, but over time, these wear parts themselves can succumb to the abrasive forces of metal ore. In this context, it is crucial to understand the significance of wear parts in metal ore impact crushers and how their proper selection and maintenance can optimize the crusher’s performance and longevity.
Wear parts in metal ore impact crushers typically include blow bars, impact plates, and liners. These components play a pivotal role in the crushing process by absorbing and redirecting the impact forces generated during the operation. As metal ore is often abrasive and hard, the wear and tear on these parts can be severe. Therefore, selecting the right materials and designs for wear parts is paramount to ensure optimal efficiency and extended service life.
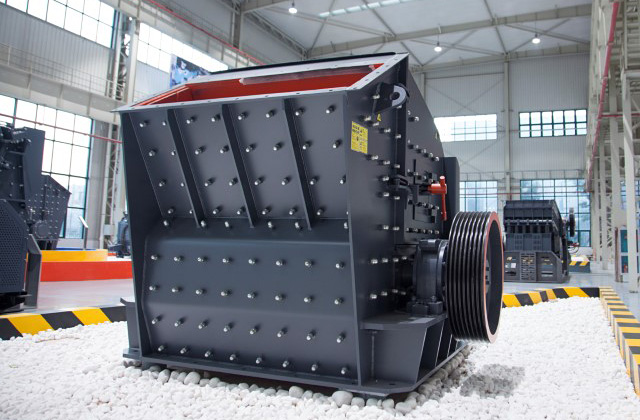
One of the primary wear parts in metal ore impact crushers is the blow bar. These are often made of high-chrome or martensitic steel to withstand the intense impact and abrasion encountered in crushing metal ores. High-chrome blow bars are known for their high wear resistance, making them suitable for applications where abrasive materials are prevalent. Martensitic steel, on the other hand, offers a balance between impact resistance and wear life, making it a versatile choice for various ore types.
Impact plates are another critical component that bears the brunt of the crushing process. These plates are positioned on the rotor of the impact crusher and are responsible for directing the material flow and absorbing impact energy. Just like blow bars, impact plates need to be made from durable materials, such as high-chrome or manganese steel, to withstand the constant pounding from metal ores.
Liners are additional wear parts that line the interior of the impact crusher’s crushing chamber. They provide protection to the crusher shell and contribute to the overall wear resistance of the machine. Liners are typically made from manganese steel, which exhibits excellent toughness and wear resistance. Regular inspection and replacement of liners are essential to prevent further damage to the crusher and maintain its efficiency.
Proper maintenance and monitoring of wear parts are crucial for maximizing the operational life of metal ore impact crushers. Regular inspections allow operators to identify signs of wear, such as reduced crushing efficiency, increased vibration, or unusual noise. Prompt replacement of worn-out parts can prevent unscheduled downtime and production interruptions.
In addition to material selection, the design and configuration of wear parts also impact the crusher’s performance. Customizing the shape and thickness of blow bars or optimizing the arrangement of liners can enhance the crusher’s efficiency in handling specific metal ores. Collaboration between crusher manufacturers and end-users is essential to tailor wear parts for specific applications, ensuring optimal performance and longevity.
The wear parts of metal ore impact crushers are critical components that directly influence the crusher’s efficiency and service life. Choosing the right materials and designs for blow bars, impact plates, and liners is essential to withstand the abrasive nature of metal ores. Regular maintenance and timely replacement of worn-out parts are crucial to prevent unplanned downtime and optimize the crusher’s overall performance. Through a combination of proper material selection, thoughtful design, and diligent maintenance, metal ore impact crushers can reliably and efficiently process ores while minimizing the impact of wear on their components.