In the realm of aggregate processing and mining operations, impact crushers play a pivotal role in reducing the size of various materials, ensuring the production of high-quality aggregates for construction projects. Among the critical parameters determining the effectiveness of an impact crusher is its production capacity. With a capacity of 350 TPH (tons per hour), these machines are engineered to deliver substantial outputs, catering to the demands of large-scale operations. This article delves into understanding the factors influencing the production capacity of impact crushers and strategies for optimizing their efficiency.
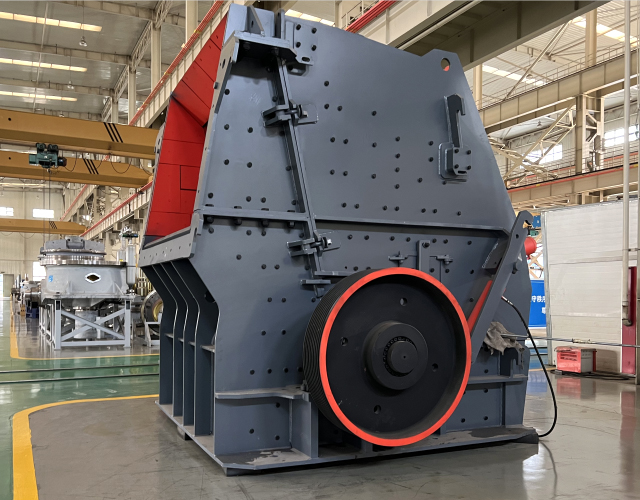
Understanding Impact Crusher Operation: Impact crushers function by utilizing the principle of impact crushing. When the material enters the crushing chamber, it encounters rapidly rotating rotor assemblies equipped with hammers or blow bars. These components impart kinetic energy to the incoming material, causing it to break upon impact against the stationary anvils or curtains. The size reduction process occurs as the material is repeatedly subjected to high-speed impacts, ultimately achieving the desired particle size distribution.
Factors Influencing Production Capacity:
- Feed Size and Gradation: The size and gradation of the feed material significantly impact the production capacity of an impact crusher. Ideally, uniform and well-graded feed materials allow for optimal utilization of the crushing chamber, resulting in higher throughput.
- Rotor Design and Speed: The design of the rotor and its rotational speed influence the kinetic energy imparted to the material. A well-designed rotor with appropriate speed ensures efficient crushing and enhanced production capacity.
- Crushing Chamber Configuration: Impact crushers offer versatility in terms of adjusting the configuration of the crushing chamber. Variations in chamber design, such as open or closed circuit configurations, impact the throughput capacity and the quality of the final product.
- Material Hardness and Abrasiveness: Harder and more abrasive materials require higher impact forces for effective reduction. Impact crushers equipped with robust components are capable of handling such materials, albeit with potential adjustments in operating parameters.
- Maintenance and Wear Parts: Regular maintenance, including inspection and replacement of wear parts such as blow bars, ensures consistent performance and prevents downtime, thereby maximizing production capacity over the equipment’s lifecycle.
Strategies for Optimizing Production Capacity:
- Proper Equipment Sizing and Selection: Ensuring that the impact crusher is appropriately sized for the application is crucial. Undersized equipment may struggle to meet the desired production targets, while oversized machines may lead to inefficiencies and increased operating costs.
- Operational Parameters Optimization: Fine-tuning operational parameters such as rotor speed, feed rate, and gap settings based on the characteristics of the feed material can optimize production capacity without compromising product quality.
- Material Pre-screening: Implementing a pre-screening process to remove fines and undersized material before it reaches the crusher can alleviate the burden on the machine, enhancing its capacity and efficiency.
- Utilization of Automation and Monitoring Systems: Integrating automation and real-time monitoring systems enables operators to closely monitor the crusher’s performance and make necessary adjustments promptly, maximizing throughput while ensuring optimal operating conditions.
- Investing in Training and Education: Providing comprehensive training to operators regarding equipment operation, maintenance practices, and troubleshooting techniques fosters proficient handling of the impact crusher, contributing to sustained productivity and longevity.
Impact crushers with a production capacity of 350 TPH represent formidable assets in the aggregate processing and mining industries. By comprehensively understanding the factors influencing production capacity and implementing strategic optimization measures, operators can unlock the full potential of these machines, ensuring consistent, high-volume production of quality aggregates to meet the demands of modern construction projects.