Mining rock jaw crusher equipment is an essential part of any mineral processing operation. This equipment is used to reduce large chunks of raw material into manageable sizes for further processing or transportation. Whether used in underground mining operations or open-pit quarries, rock jaw crushers play a crucial role in productivity and efficiency. In this article, we’ll explore the significance of rock jaw crusher equipment in mining operations and highlight some key considerations for purchasing such equipment.
First and foremost, rock jaw crushers are renowned for their robustness and reliability in the mining industry. They are designed to withstand the harsh conditions encountered in mining environments, including high-impact forces, abrasive materials, and continuous operation. Their sturdy construction and heavy-duty components make them capable of handling the toughest materials, such as granite, basalt, and iron ore.
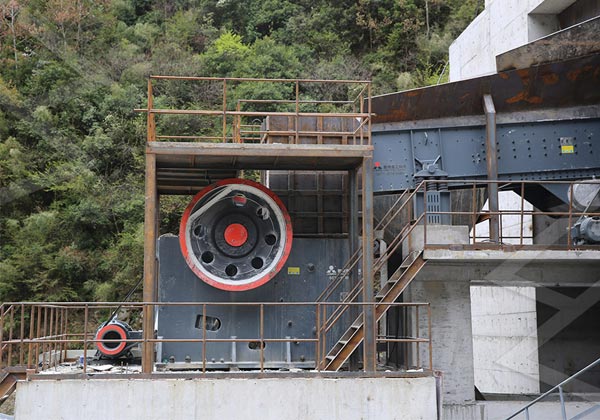
One of the primary functions of a rock jaw crusher is to break down large rocks into smaller pieces. This is achieved through the use of a fixed jaw and a movable jaw, which exert compressive forces on the rock material. As the material is fed into the crusher, it is crushed between the jaws and discharged at the bottom, resulting in smaller-sized fragments suitable for further processing.
In addition to size reduction, rock jaw crushers are also capable of producing a uniform product size, which is essential for downstream processing operations. This ensures consistent quality and facilitates the efficient extraction of valuable minerals from the ore. Furthermore, some jaw crushers offer adjustable settings, allowing operators to control the size of the final product according to specific requirements.
When purchasing rock jaw crusher equipment for mining operations, several factors should be taken into consideration to ensure optimal performance and longevity. One crucial aspect is the capacity of the crusher, which determines the maximum throughput or the amount of material that can be processed per unit of time. It’s essential to select a crusher with sufficient capacity to meet the production demands of the operation.
Another important consideration is the size of the feed opening, which dictates the maximum size of the feed material that the crusher can accept. Choosing a jaw crusher with a wide feed opening allows for the processing of larger rocks, resulting in higher productivity and reduced downtime associated with blockages.
Additionally, the efficiency of the crushing chamber and the angle of the jaw plates play a significant role in determining the performance of the crusher. A well-designed crushing chamber ensures optimal crushing efficiency and reduces the occurrence of wear and tear on the jaw plates, prolonging their lifespan.