A hydraulic cone crusher is a type of crushing equipment used in mining, metallurgy, construction, and other industries. It utilizes hydraulic pressure to compress and crush materials between the mantle and concave. This type of crusher is known for its efficiency, high crushing capacity, and reliability. In this technical overview, we’ll delve into the key components, working principle, and technical specifications of a typical hydraulic cone crusher.
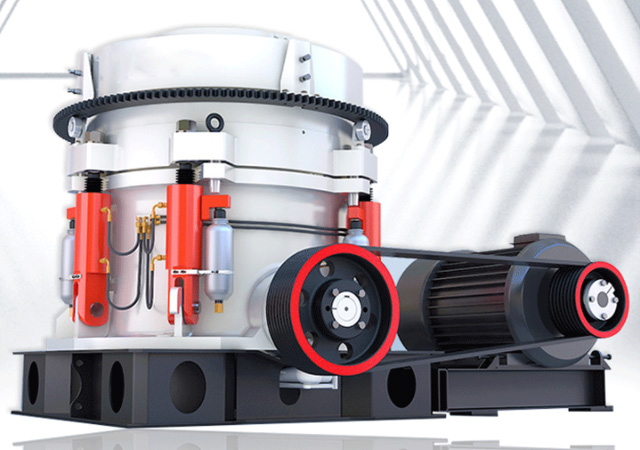
Components:
- Main Frame: The main frame of a hydraulic cone crusher provides structural support and houses the other components.
- Mantle and Concave: These are the wear-resistant parts that form the crushing chamber. The mantle is fixed to the main shaft, and the concave is fixed to the frame. They form the crushing cavity where the material is crushed.
- Hydraulic System: This system provides the hydraulic pressure necessary for the crusher’s operation. It includes hydraulic cylinders, hydraulic motors, hydraulic pumps, and hydraulic control valves.
- Main Shaft: The main shaft is responsible for transmitting power from the motor to the crushing cone. It rotates eccentrically, causing the mantle to oscillate, thereby crushing the material.
- Drive System: The drive system consists of an electric motor, a transmission system (such as V-belts or direct drive), and a flywheel. It provides the necessary power to drive the crusher.
- Feed Hopper: The feed hopper is a large opening where the raw material is fed into the crusher. It typically includes a vibrating feeder to regulate the flow of material into the crushing chamber.
- Adjustment Ring: The adjustment ring allows for the adjustment of the crusher’s discharge opening size. This enables the operator to control the size of the crushed product.
Working Principle:
- Crushing Process: When the hydraulic cone crusher is in operation, the motor drives the eccentric shaft to rotate through a horizontal shaft and a pair of bevel gears. This rotation causes the main shaft and mantle to move eccentrically, creating a crushing motion.
- Material Feed: Raw material enters the crushing chamber through the feed hopper and is fed into the crushing cavity between the mantle and concave.
- Crushing Action: As the mantle moves eccentrically, it compresses the material against the concave, effectively crushing it into smaller pieces.
- Hydraulic Adjustment: The hydraulic system controls the positioning of the main shaft and mantle, allowing for the adjustment of the crusher’s discharge opening size. This adjustment ensures the desired product size and shape.
- Overload Protection: Hydraulic cylinders provide overload protection by releasing pressure in the event of a tramp metal or uncrushable material entering the crushing chamber.
Technical Specifications:
- Capacity: Hydraulic cone crushers are available in various sizes and capacities, ranging from tens of tons per hour to thousands of tons per hour, depending on the model and application.
- Crushing Efficiency: Hydraulic cone crushers are known for their high crushing efficiency, which is achieved through the optimized design of the crushing chamber and the use of high-quality wear-resistant materials.
- Power Requirements: The power requirements of a hydraulic cone crusher depend on factors such as the size of the crusher, the type of material being crushed, and the desired product size. Typically, hydraulic cone crushers are powered by electric motors ranging from tens to hundreds of kilowatts.
- Adjustment Range: The adjustment range of the crusher’s discharge opening size varies depending on the model and design. It can typically range from a few millimeters to several centimeters.
- Safety Features: Hydraulic cone crushers are equipped with various safety features to protect the crusher and its operators. These may include hydraulic overload protection, automatic lubrication systems, and emergency stop buttons.
Hydraulic cone crushers are versatile and efficient crushing machines used in various industries. Their robust construction, high crushing capacity, and reliable performance make them ideal for processing a wide range of materials. Understanding their key components, working principle, and technical specifications is essential for maximizing their productivity and longevity.