The jaw crusher stands as a stalwart in the realm of quarrying, an indispensable workhorse in the process of extracting raw materials from the earth’s crust. Its ubiquity in quarries worldwide is a testament to its efficacy, reliability, and versatility. This article delves into the intricacies of the jaw crusher, exploring its fundamental principles, applications, and the pivotal role it plays in the quarrying industry.
At its core, the jaw crusher is a mechanical device designed to break down large rocks into smaller, more manageable fragments. Its operation relies on the principle of compression, where the raw material is fed into the crushing chamber and subjected to immense pressure exerted by a fixed jaw and a movable jaw. This dynamic interaction between the jaws effectively pulverizes the incoming material, reducing it to the desired size for further processing.
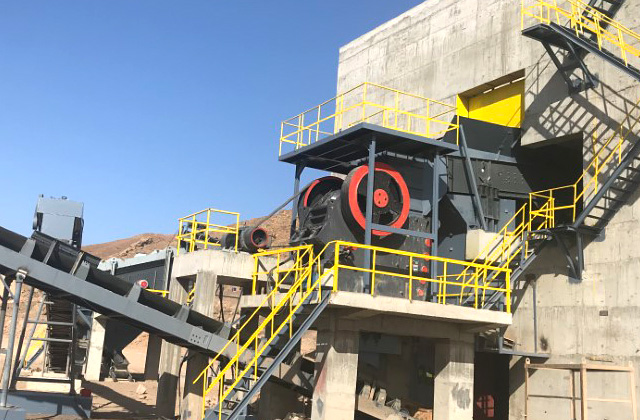
One of the key advantages of the jaw crusher lies in its ability to handle a wide range of materials, from soft limestone to hard granite and everything in between. This versatility makes it a go-to solution for quarry operators dealing with diverse geological formations and varying material properties. Whether it’s primary crushing at the quarry face or secondary crushing downstream in the processing plant, the jaw crusher excels in delivering consistent performance across different applications.
Furthermore, the jaw crusher boasts robust construction, engineered to withstand the rigors of heavy-duty quarrying operations. Its sturdy frame, reinforced bearings, and durable components ensure long-term reliability even in the harshest working environments. This rugged design not only enhances operational uptime but also minimizes maintenance requirements, translating into cost savings for quarry operators.
In addition to its primary function of crushing rocks, the jaw crusher offers versatility through its adjustable settings. Operators can fine-tune parameters such as the gap width and eccentricity to optimize the crushing process for specific material types and desired end products. Whether producing aggregates for construction projects or finely crushed minerals for industrial applications, the jaw crusher can be tailored to meet the exacting requirements of the quarrying operation.
Moreover, advancements in technology have propelled the evolution of the jaw crusher, introducing features that enhance efficiency, productivity, and safety. Modern models may incorporate automation systems, such as hydraulic adjustment mechanisms and remote monitoring capabilities, streamlining operation and minimizing downtime. Furthermore, innovations in materials and design techniques have led to improvements in energy efficiency and reduced environmental impact, aligning with the industry’s sustainability goals.