A large capacity, low-cost cone crusher is a crucial piece of equipment in various industries, especially in mining, aggregates, and construction. Cone crushers are widely used due to their efficient crushing action, high reduction ratio, and versatility in handling various types of materials.
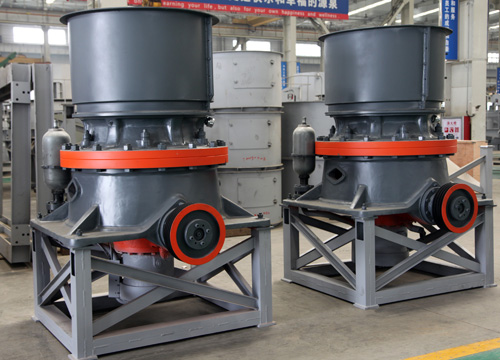
To achieve large capacity, engineers focus on several key design elements:
- Size and Geometry of Crushing Chamber: A larger chamber allows for more material to be processed at once, increasing throughput. The geometry of the chamber also plays a crucial role in ensuring efficient crushing and uniform product size distribution.
- Power and Drive System: A robust power system is essential for handling the high loads encountered in large-scale crushing operations. High horsepower motors and efficient drive systems are employed to provide the necessary torque and speed to crush the toughest materials.
- Eccentric Design: The eccentric mechanism in a cone crusher is responsible for generating the crushing action. Optimizing the design of the eccentric ensures that the crusher can handle large volumes of material while maintaining a uniform crushing force across the entire chamber.
- Liner Design: The liners inside the crushing chamber wear over time and must be replaced regularly to maintain optimal performance. Manufacturers employ advanced materials and designs to maximize the lifespan of the liners and minimize downtime for maintenance.
- Automation and Control Systems: Automation technology can improve the efficiency and reliability of cone crushers by optimizing processes such as material feed, crusher setting adjustments, and monitoring of operating parameters. This reduces the risk of human error and ensures consistent performance.
In addition to large capacity, achieving low cost involves optimizing various aspects of the cone crusher design and manufacturing process:
- Material Selection: Using high-quality materials for critical components such as the crushing chamber, eccentric, and wear liners ensures durability and longevity, reducing the need for frequent replacements and maintenance.
- Manufacturing Efficiency: Streamlining the manufacturing process and utilizing advanced machining techniques help reduce production costs without compromising quality. Lean manufacturing principles and automation can improve efficiency and lower labor costs.
- Energy Efficiency: Designing the cone crusher for optimal energy efficiency helps reduce operating costs over the equipment’s lifespan. This includes minimizing energy losses in the drive system, optimizing crushing chamber geometry to reduce energy consumption per ton of material processed, and incorporating energy-saving technologies such as variable speed drives.
- Serviceability and Maintenance: Easy access to key components for maintenance and servicing reduces downtime and associated costs. Design features such as hydraulic adjustment systems and removable liners simplify maintenance tasks, allowing for quicker turnaround times and lower labor expenses.
- Total Cost of Ownership (TCO): Manufacturers and operators consider the TCO of the cone crusher, which includes not only the initial purchase price but also operating costs, maintenance expenses, and expected lifespan. By optimizing design and operational parameters to minimize TCO, manufacturers can offer cone crushers with low cost per ton crushed.
In summary, achieving large capacity and low cost in a cone crusher requires a holistic approach that considers factors such as design optimization, material selection, manufacturing efficiency, and operational performance. By addressing these aspects comprehensively, manufacturers can deliver cone crushers that meet the demanding requirements of modern mining and aggregate operations while remaining cost-effective.