Introduction:
The cement industry plays a crucial role in the construction sector, providing the essential building material required for infrastructure development. Cement grinding plants are an integral part of the cement manufacturing process, where clinker, the main component of cement, is ground into a fine powder. This powder, known as cement, is used in various construction applications, such as building foundations, roads, bridges, and dams.
Project Scope and Objectives:
The primary objective of a cement grinding plant project is to establish a facility capable of grinding clinker into high-quality cement. The project scope typically includes the construction of a grinding mill, storage silos for clinker and additives, material handling equipment, and necessary infrastructure such as power supply and water sources.
Site Selection:
Selecting the appropriate location for the grinding plant is a critical decision that considers factors like proximity to the raw material source, transportation accessibility, availability of utilities, and environmental regulations. Ideally, the site should be situated close to a cement production facility or a clinker source, reducing transportation costs and ensuring a steady supply of raw materials.
Plant Design and Layout:
The plant design and layout are determined by factors such as production capacity, available land area, and environmental considerations. The grinding mill, the heart of the plant, should be designed to efficiently and effectively grind clinker into the desired fineness. It is essential to select the right type of mill, such as ball mills or vertical roller mills, depending on the project requirements and the availability of suitable technology.
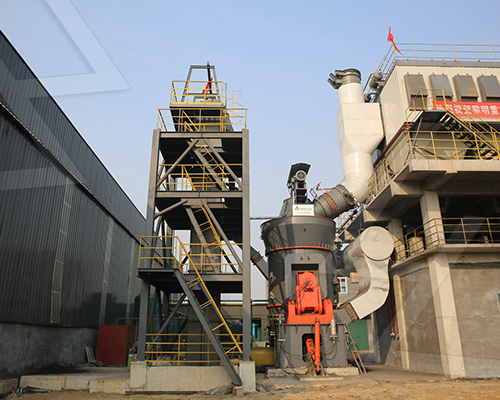
Process Flow:
The process flow of a cement grinding plant involves several stages. First, clinker, along with gypsum and other additives, is transported from the storage silos to the grinding mill. The clinker is ground to a fine powder, resulting in cement. The finished cement is then stored in silos or dispatched for distribution. The process flow should be optimized to ensure a consistent and high-quality product.
Environmental Considerations:
Cement production can have environmental impacts, so it is crucial to address these concerns during the project design and operation. Dust control measures, such as dust collectors and bag filters, should be implemented to minimize air pollution. Additionally, proper waste management and water conservation techniques should be incorporated to reduce the project’s environmental footprint.
Project Timeline and Cost:
A cement grinding plant project typically requires a well-defined project timeline and budget. The timeline should include activities like site preparation, construction, equipment installation, and commissioning. The cost estimation should consider factors such as land acquisition, plant construction, machinery procurement, labor, and operational expenses.
Project Benefits:
The successful completion of a cement grinding plant project brings several benefits. It contributes to the local economy by creating employment opportunities during construction and operation. Moreover, it strengthens the cement supply chain, ensuring a steady and reliable source of cement for the construction industry. The project also supports infrastructure development, as cement is a fundamental material for various construction projects.
Conclusion:
A cement grinding plant project is a significant endeavor that requires careful planning, design, and execution. The successful implementation of such a project ensures the availability of high-quality cement for the construction industry, supporting economic growth and infrastructure development. By considering the various aspects discussed in this overview, stakeholders can embark on a cement grinding plant project with confidence and achieve their objectives efficiently.