The primary crushing process of iron ore refers to the first step of reducing large-sized iron ore materials into smaller particles. It plays a crucial role in the entire iron ore processing flowchart. The process involves various types of crushers, which utilize different principles and mechanisms to achieve the desired size reduction. In this response, I will provide a detailed explanation of the primary crushing process of iron ore.
Iron ore is a mineral that is extracted from the earth’s crust in large deposits. It contains iron oxides, primarily hematite (Fe2O3) and magnetite (Fe3O4), along with other minerals and impurities. Before the iron ore can be used in the production of steel or other applications, it needs to undergo several processing stages, including primary crushing.
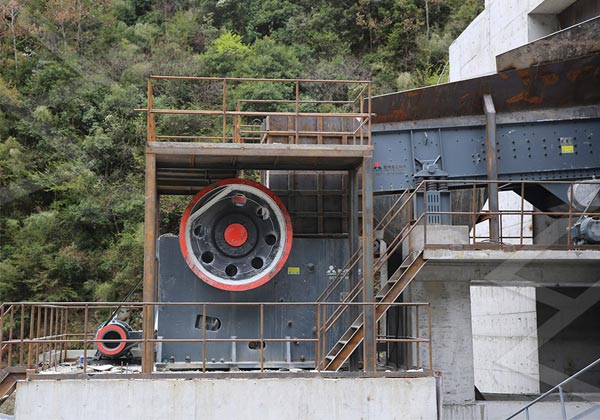
The primary crushing process aims to break down the large-sized iron ore rocks into smaller particles that can be handled and processed more efficiently. Typically, the iron ore rocks are first blasted and extracted from open-pit mines or underground mines using drilling and blasting techniques. Once the ore is extracted, it is transported to the primary crusher, which is usually located near the mine site.
Various types of crushers are commonly used for primary crushing of iron ore. The selection of the specific crusher depends on the characteristics of the ore, such as its hardness, size, and moisture content, as well as the desired final product size. Some of the commonly used crushers for primary crushing of iron ore include jaw crushers, gyratory crushers, and cone crushers.
Jaw crushers are the most common type of crusher used in primary crushing operations. They consist of a fixed plate and a movable plate, with the ore being fed into the space between the plates. The movable plate moves back and forth, exerting pressure on the ore, and breaking it into smaller pieces. Jaw crushers are known for their high capacity and efficiency in breaking down even the hardest ores.
Gyratory crushers are another type of primary crusher used in some iron ore processing plants. They have a conical-shaped crushing head that gyrates around a fixed point, causing the ore to be crushed between the crushing head and the stationary walls of the crusher. Gyratory crushers are often used when the ore is hard and abrasive.
Cone crushers are also utilized in some iron ore processing plants for primary crushing. They have a cone-shaped crushing chamber that tapers down toward the discharge end. The ore is fed into the top of the cone crusher and is crushed between the mantle and the concave.
After the primary crushing stage, the crushed iron ore particles are then conveyed to further processing stages, such as secondary crushing, grinding, and beneficiation. Secondary crushing processes aim to further reduce the size of the particles, while grinding processes involve reducing the particle size through mechanical forces. Beneficiation processes, such as magnetic separation or flotation, are used to separate the valuable iron ore minerals from the gangue minerals.