Rock crushers play a crucial role in the mining and construction industries, breaking down large stones into smaller particles for various applications. The efficiency of rock crusher production is a critical factor in determining the success of mining and construction projects. This analysis will delve into the key aspects that impact rock crusher production, including factors affecting productivity, optimization strategies, and the importance of maintenance.
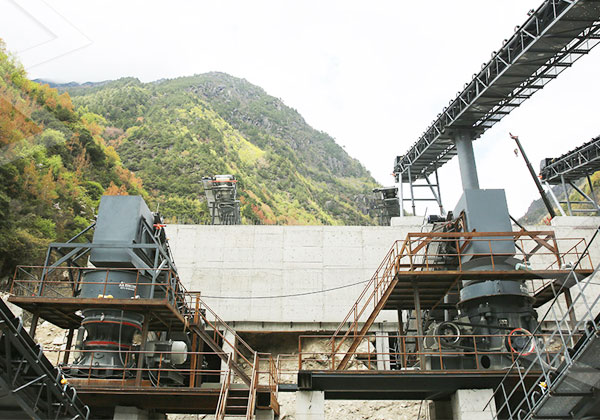
Factors Affecting Rock Crusher Production:
Feed Size and Gradation: The size and gradation of the input material significantly influence the crushing process. Ideally, uniform feed size enables the crusher to work efficiently, reducing the risk of overloading and wear. Inconsistent feed sizes may lead to production bottlenecks and lower throughput.
Crusher Design and Parameters: The type of crusher and its design affect production. Jaw crushers, impact crushers, and cone crushers have distinct crushing mechanisms. Choosing the right type and adjusting parameters, such as closed-side setting and throw, optimize the production process.
Operating Conditions: Environmental factors, such as ambient temperature, humidity, and altitude, can impact crusher performance. Extreme conditions might require additional precautions or specialized equipment to maintain consistent production rates.
Material Hardness and Abrasiveness: The hardness and abrasiveness of the rocks being crushed influence wear and tear on the crusher components. Harder materials demand more energy and may lead to increased maintenance and downtime.
Optimization Strategies for Enhanced Production:
Regular Maintenance: A well-maintained crusher ensures maximum efficiency and extends the machine’s lifespan. Lubrication, inspection of wear parts, and timely replacements minimize downtime and prevent major breakdowns.
Automation and Control Systems: Implementing automation and advanced control systems optimize crusher performance. These technologies can regulate feed rate, adjust settings, and monitor vital parameters in real-time, leading to improved production and reduced energy consumption.
Crushing Chamber Optimization: The shape of the crushing chamber affects the capacity and product quality. By optimizing the chamber design, manufacturers can achieve better particle shape and size distribution, enhancing the final product’s market value.
Scalping and Screening: Incorporating efficient scalping and screening processes remove fines and unnecessary material before reaching the crusher. This minimizes wear on the crusher and enhances overall production efficiency.