A jaw crusher is a primary crushing machine used for breaking large stones or rocks into smaller pieces. It is widely used in various industries, including mining, construction, and recycling. To ensure the efficiency and reliability of a jaw crusher, manufacturers and users adhere to standard specifications. In this article, we will outline the standard specifications for a typical jaw crusher.
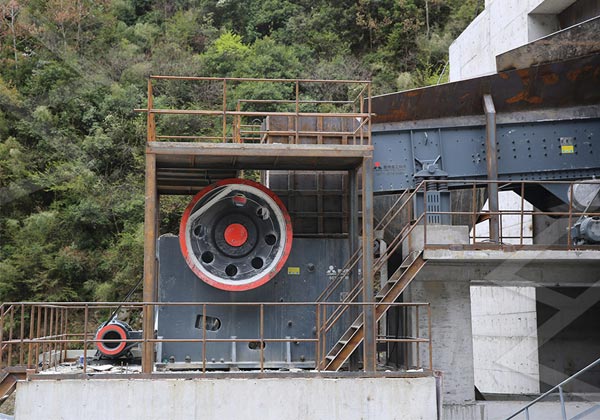
Machine Design and Dimensions:
The jaw crusher typically consists of two vertical jaws, one fixed and the other movable. The fixed jaw is mounted on a rigid frame, while the movable jaw is attached to an eccentric shaft with a flywheel at one end. The size and dimensions of the jaw crusher vary based on the specific application, but a standard jaw crusher is usually around 1 to 1.5 meters wide and 2.5 to 3 meters long.
Capacity and Feed Opening:
The capacity of a jaw crusher refers to the maximum amount of material it can process in a given time period. It is typically measured in tons per hour (TPH). The capacity depends on various factors such as the type of feed material, the size distribution of the feed, the setting of the crusher, and the physical properties of the rock or ore being crushed. The feed opening is the dimension of the jaw crusher’s inlet through which the material enters the crushing chamber. It is usually expressed in millimeters.
Crushing Mechanism:
The standard jaw crusher uses a compression mechanism to crush the material. The two jaws come together, and the material is progressively crushed into smaller sizes as it moves down the crushing chamber. A double-toggle jaw crusher is commonly used, where the swinging jaw moves forward and backward, whereas a single-toggle jaw crusher has only one swing jaw.
Power and Drive System:
The jaw crusher is typically powered by an electric motor or a diesel engine. The power rating of the motor or engine depends on the size and capacity of the crusher. The drive system may consist of V-belts, pulleys, and a flywheel to provide inertia for smoother operation.
Discharge Gap Adjustment:
The discharge gap, also known as the closed-side setting (CSS), determines the final product size. By adjusting the gap between the two jaws, the size of the crushed material can be controlled. The standard jaw crushers feature a mechanical or hydraulic system for adjusting the CSS.
Safety Features:
Jaw crushers must incorporate several safety features to protect operators and maintenance personnel. These may include safety guards for moving parts, emergency stop buttons, and interlock systems to prevent the crusher from starting when the guards are not in place.
Materials and Wear Parts:
The jaws of the crusher are often made from manganese steel, which provides excellent wear resistance. Other wear parts, such as jaw plates and liners, are also made from high-quality materials to prolong the life of the machine and reduce maintenance costs.
Lubrication and Cooling:
Proper lubrication is essential for the smooth operation of the jaw crusher. The machine must have a reliable lubrication system to ensure all moving parts are adequately lubricated. Additionally, some crushers may require cooling systems to prevent overheating during prolonged operation.
Environmental Considerations:
Manufacturers often design jaw crushers to comply with environmental regulations and noise emission standards. Dust suppression systems may be incorporated to control dust generation during crushing.