A vibrating screen is a mechanical device that utilizes various vibrating and shaking motions to sort, separate, or classify different particles based on size or other characteristics. It finds application in a variety of industries, including mining, food processing, pharmaceuticals, chemical, and many others. The primary purpose of a vibrating screen is to separate materials into different fractions, typically by size, to enhance the efficiency of subsequent processing steps or to obtain a desired particle size distribution.
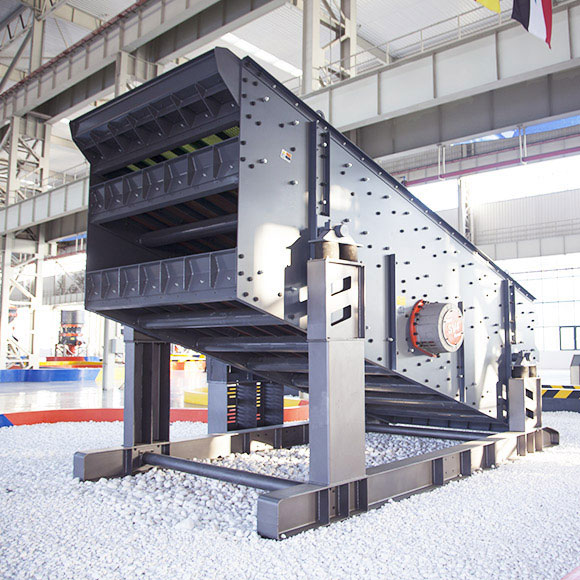
Operation of a Vibrating Screen:
Material Feeding: The material to be screened is fed onto the vibrating screen’s surface. This can be done using conveyors, chutes, or other feeding mechanisms.
Screening Surface: The vibrating screen consists of a screen surface with different types of openings or perforations that allow particles of certain sizes to pass through while blocking larger particles.
Vibration Generation: Vibrations are generated either by mechanical means (such as eccentric shafts with unbalanced weights) or by electromagnetic means (using electromagnetic vibrators). These vibrations cause the screen surface to shake, resulting in the movement of particles.
Screening Process: As the screen surface vibrates, the particles move and interact with the openings or perforations. Smaller particles that are smaller than the openings can pass through, while larger particles are unable to pass and remain on the screen surface.
Separation and Sorting: The particles that pass through the openings are collected as the undersize fraction, while the particles that are retained on the screen surface are collected as the oversize fraction. This separation process effectively classifies the particles based on size.
Discharge: The separated fractions are discharged from different outlets or discharge points on the vibrating screen. The undersize fraction can be directed to further processing or collection, and the oversize fraction can be directed for reprocessing or disposal.
Principles of Vibrating Screen Operation:
Vibration Mechanism: The heart of a vibrating screen is its vibration mechanism, which generates the necessary vibratory motion. This mechanism can be driven by unbalanced weights, eccentric shafts, gears, or electromagnetic vibrators. The motion generated by the vibration mechanism can be circular, linear, elliptical, or a combination of these, depending on the design and application.
Screening Surface Design: The design of the screen surface, including the size and shape of openings or perforations, influences the screening efficiency and the particle size distribution of the separated fractions. Screens can have various configurations, such as woven wire mesh, punched plate, polyurethane panels, or other specialized designs.
Angle of Inclination: The angle at which the vibrating screen is inclined also plays a significant role in its operation. The angle affects the material’s movement on the screen surface, impacting the separation efficiency and throughput.
Frequency and Amplitude: The frequency (number of vibrations per unit of time) and amplitude (the distance the screen surface moves during each vibration) of the vibrating screen can be adjusted to optimize the screening process. Higher frequency and amplitude can improve separation efficiency, while lower values may be suitable for delicate or fine materials.
Screening Efficiency: The efficiency of a vibrating screen is determined by its ability to effectively separate particles of different sizes. Factors such as vibration frequency, amplitude, angle of inclination, and screen design all contribute to the overall efficiency.