Designing a rock crusher layout in Kenya involves careful consideration of various factors to ensure optimal functionality, efficiency, and safety. A well-thought-out layout can contribute significantly to the success of a rock crushing plant by maximizing production, minimizing downtime, and ensuring worker safety.
One of the primary considerations when designing a rock crusher layout is the geology of the site. Understanding the type and hardness of the rocks to be crushed is crucial, as it directly impacts the choice of crushers, screens, and other equipment. For instance, if the site contains hard granite, the equipment needs to be capable of handling high compression forces.
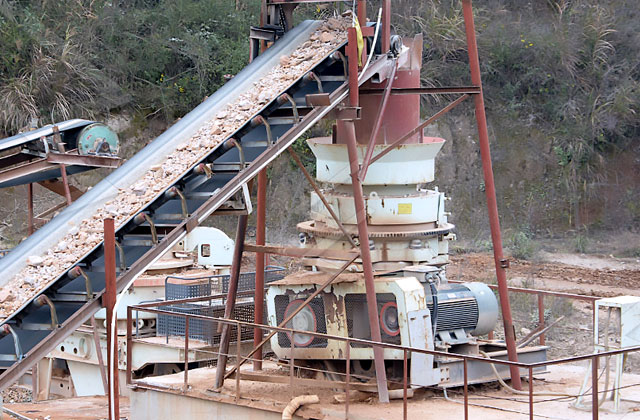
The layout should be planned in a way that takes advantage of the natural terrain, minimizing the need for excessive excavation and earthwork. This not only reduces costs but also helps blend the facility into the environment. Additionally, the proximity to the source of raw materials should be considered to minimize transportation distances.
A typical rock crusher layout includes primary and secondary crushers, screens, and conveyors. The primary crusher is responsible for reducing the size of the rocks from the quarry to a size that can be handled by the secondary crusher. The primary crusher should be located close to the pit entrance to reduce hauling costs and accommodate efficient transportation of raw material.
The secondary crusher further reduces the size of the crushed material and prepares it for the next stages of processing. It’s important to choose the right type of secondary crusher based on factors like the required end product size and capacity.
Screens are integral to the rock crusher layout as they separate the crushed material into different sizes for further processing. Efficient screening ensures that only the appropriate sizes are sent for further crushing or final use. Proper placement of screens is necessary to optimize the screening process and prevent material bottlenecks.
Conveyors play a critical role in transporting material between different stages of the crushing process. Their layout should be designed for smooth material flow, minimizing the risk of blockages and optimizing efficiency. Conveyors should be placed at a suitable height to allow for easy maintenance access underneath.
Safety is paramount in any layout design. Adequate space should be allocated for walkways, platforms, and emergency access. Safety guards and barriers should be installed where necessary to protect workers from moving parts of the machinery. Additionally, dust control measures should be integrated into the layout to mitigate the health risks associated with airborne particles.