A cement plant’s designated industrial mill is a crucial component of the manufacturing process, playing a pivotal role in the production of cement. This industrial mill is typically a ball mill, roller press, or vertical roller mill, and it is responsible for grinding raw materials into fine powders that will ultimately be transformed into the durable and essential building material we know as cement. In this essay, we will explore the significance of the designated industrial mill in a cement plant, its operation, and its role in cement production.
The industrial mill is the heart of a cement plant, where various raw materials such as limestone, clay, shale, iron ore, and silica are finely ground into a homogenous powder known as raw meal. The quality and consistency of this raw meal are vital for the quality and performance of the final cement product. The mill operates continuously, 24 hours a day, seven days a week, and its efficiency and reliability are critical to the overall productivity of the cement plant.
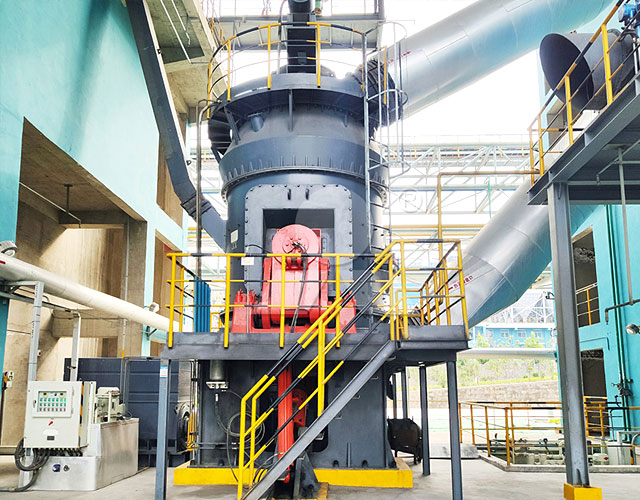
One of the primary functions of the industrial mill is to reduce the particle size of raw materials to a level where they can be efficiently combined in the next stages of the cement manufacturing process, namely, the preheating, calcination, and clinkerization processes. Grinding the raw materials to a fine powder increases their surface area, making them more reactive during the subsequent chemical reactions. This finely ground raw meal is then mixed with other additives, such as gypsum, to regulate the setting time of the cement.
The industrial mill’s operation involves the use of large grinding balls or rollers that crush and grind the raw materials into the desired consistency. Depending on the type of mill used, it may operate in a closed or open circuit. In a closed-circuit system, the ground material is separated from the coarse particles, which are then recycled back into the mill for further grinding, ensuring efficient use of energy and resources.
The choice of the industrial mill type depends on various factors, including the characteristics of the raw materials, the desired quality of the final cement product, and energy efficiency considerations. Ball mills are commonly used in cement plants, where the raw materials are ground in rotating cylindrical drums filled with grinding media (steel balls). Roller presses and vertical roller mills are newer technologies that offer advantages such as lower energy consumption and a smaller environmental footprint.
Efficient operation and maintenance of the industrial mill are essential to ensure the continuous production of high-quality cement. Regular inspections, lubrication, and monitoring of key parameters like grinding pressure, temperature, and airflow are crucial for preventing downtime and optimizing performance.
The designated industrial mill in a cement plant plays a central role in the production of cement by grinding raw materials into a fine powder. It is a critical piece of equipment that impacts the quality, efficiency, and environmental sustainability of the cement manufacturing process. The choice of mill type, its proper operation, and maintenance are key factors in ensuring the success of a cement plant and the production of a reliable and durable building material that is essential for construction and infrastructure development worldwide.