Impact crushers are crucial equipment in industries like mining, construction, and recycling. They are designed to break down large rocks, concrete, and other materials into smaller, more manageable pieces. Over time, the wearing parts of an impact crusher can wear out due to the abrasive nature of the materials being processed. When this happens, it is crucial to replace these wearing parts to ensure the crusher’s optimal performance and longevity. In this article, we will discuss the replacement of wearing parts in impact crushers, including the types of wearing parts, the replacement process, and the importance of regular maintenance.
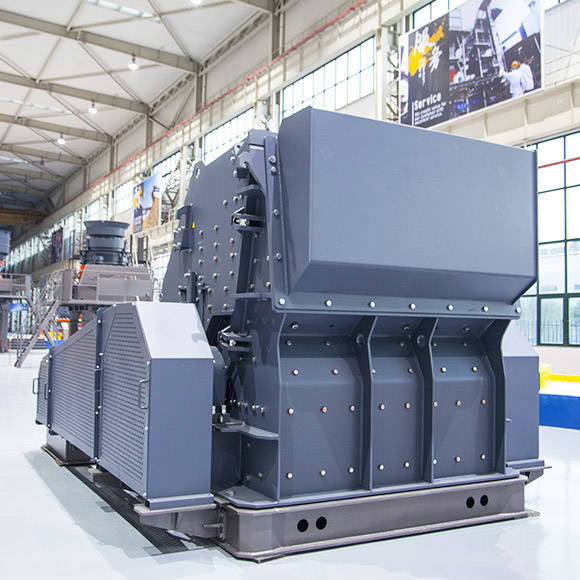
Importance of Replacing Wearing Parts:
Impact crushers operate under extreme conditions, subjecting their various components to significant wear and tear. The wearing parts of an impact crusher are vital for its efficient and safe operation. Failing to replace these parts when needed can result in decreased productivity, increased maintenance costs, and even safety hazards for the operators and those working around the machine.
Types of Wearing Parts in Impact Crushers
Impact crushers consist of various components that work together to crush materials effectively. Some of the key wearing parts in an impact crusher include:
Blow Bars: These are the primary wearing parts in an impact crusher. Blow bars are typically made of high-strength materials like manganese steel or chrome steel. They are responsible for delivering the impact force to the material being crushed.
Impact Plates: Impact plates are wear-resistant plates located on the inner surface of the impact crusher’s chamber. They protect the housing and other internal components from wear and tear caused by the material’s impact.
Rotor Assembly: The rotor is a critical component that houses the blow bars. Over time, the rotor may experience wear and require replacement.
Bearings: Bearings support the rotation of the rotor and other moving parts. If the bearings wear out, they should be replaced to prevent further damage to the crusher.
Replacement Process for Wearing Parts
Replacing wearing parts in an impact crusher requires careful planning and execution to ensure the crusher’s continued functionality. Here is a step-by-step guide to the replacement process:
Safety First: Before starting any maintenance or replacement work, ensure the impact crusher is safely powered off and all energy sources are locked out.
Access the Wearing Parts: Depending on the crusher’s design, you may need to remove protective covers or access doors to reach the wearing parts.
Remove Old Wearing Parts: Carefully remove the worn-out blow bars, impact plates, or other components. Be cautious not to damage the crusher’s interior during this process.
Inspect Other Components: While the crusher is open, it’s a good practice to inspect other components, such as the rotor, bearings, and belts, for signs of wear or damage. Replace any worn or damaged parts.
Select and Install New Parts: Choose high-quality replacement parts designed for your specific impact crusher model. Follow the manufacturer’s instructions for the correct installation of new wearing parts.
Balancing and Alignment: Ensure the rotor and other moving parts are properly balanced and aligned to prevent vibrations and uneven wear on the new parts.
Testing and Calibration: After replacing the wearing parts, run the impact crusher and monitor its performance. Make any necessary adjustments to ensure optimal crushing efficiency.
Regular Maintenance: Implement a routine maintenance schedule to inspect and replace wearing parts as needed to extend the crusher’s lifespan and maintain its productivity.
The replacement of wearing parts in impact crushers is a critical maintenance task that ensures the crusher’s longevity and efficient operation. By understanding the types of wearing parts, following a systematic replacement process, and prioritizing regular maintenance, operators can maximize the performance and reliability of their impact crushers, ultimately contributing to the success of their crushing operations.