A metal ore crusher process control system is a critical component of the mining and mineral processing industry. It plays a crucial role in optimizing the production process, ensuring efficient utilization of resources, and enhancing safety. In this article, we will discuss the key aspects of a metal ore crusher process control system.
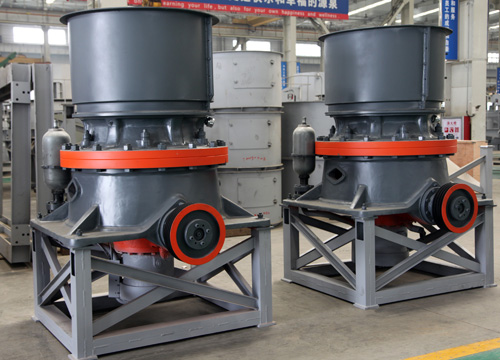
Automation and Control:
Modern metal ore crusher process control systems are highly automated, utilizing advanced technologies such as PLCs (Programmable Logic Controllers), SCADA (Supervisory Control and Data Acquisition) systems, and DCS (Distributed Control Systems) to monitor and control various aspects of the crushing process. These systems help in achieving consistent and precise control over the crushers and associated equipment.
Real-time Monitoring:
One of the primary functions of a process control system is real-time monitoring. Sensors placed at critical points in the crushing circuit continuously collect data on various parameters such as ore feed rate, crusher power consumption, conveyor belt speeds, and crusher chamber pressure. This data is then transmitted to the control system, where it is analyzed to ensure the crusher operates within its design parameters.
Optimal Feed Control:
Controlling the feed rate of ore into the crusher is essential for maintaining stable and efficient operation. Process control systems use feedback loops to adjust the ore feed rate based on the crusher’s current load and performance. This helps prevent overloading or underloading the crusher, optimizing its throughput and minimizing wear and tear.
Crusher Setting Adjustment:
Metal ore crushers often have adjustable settings to control the size of the crushed product. The process control system can automatically adjust these settings based on factors like ore hardness and desired product specifications. This ensures that the crusher consistently produces the required product size while minimizing energy consumption.
Emergency Shutdown and Safety:
Process control systems are equipped with safety features to respond to abnormal conditions. If a critical parameter exceeds a predefined threshold, the system can initiate an emergency shutdown to prevent equipment damage or personnel injury. Additionally, safety interlocks can be implemented to ensure that crushers cannot operate in unsafe conditions.
Energy Efficiency:
Efficient energy usage is a crucial consideration in the operation of metal ore crushers. Process control systems help optimize power consumption by regulating various crusher parameters, such as the speed of the crushing chamber, to match the current load and feed conditions. This results in reduced energy costs and a smaller environmental footprint.
Remote Monitoring and Control:
In many cases, metal ore crusher process control systems can be accessed remotely, allowing operators to monitor and control the crushing process from a central control room. This remote capability enhances operational flexibility and allows for timely responses to changing conditions or issues.
Scalability and Adaptability:
Metal ore crusher process control systems should be scalable and adaptable to accommodate changes in production requirements or the addition of new equipment. Upgrades and modifications can be made to the system as needed to meet evolving operational needs.
Metal ore crusher process control system is a critical tool in the mining and mineral processing industry. It enables automation, real-time monitoring, safety, and efficiency in the ore crushing process, ultimately contributing to higher production yields and reduced operational costs. As technology continues to advance, these systems will play an even more significant role in optimizing ore processing operations.