Designing a professional large-capacity cone crusher is a complex engineering task that requires careful consideration of various factors, including material processing requirements, energy efficiency, safety, and reliability. This essay will outline the key design aspects and considerations for developing a high-capacity cone crusher.
Introduction
Cone crushers are widely used in the mining and construction industries for crushing hard and abrasive materials. A large-capacity cone crusher is essential for efficient and productive operations, as it can process substantial amounts of material quickly and effectively.
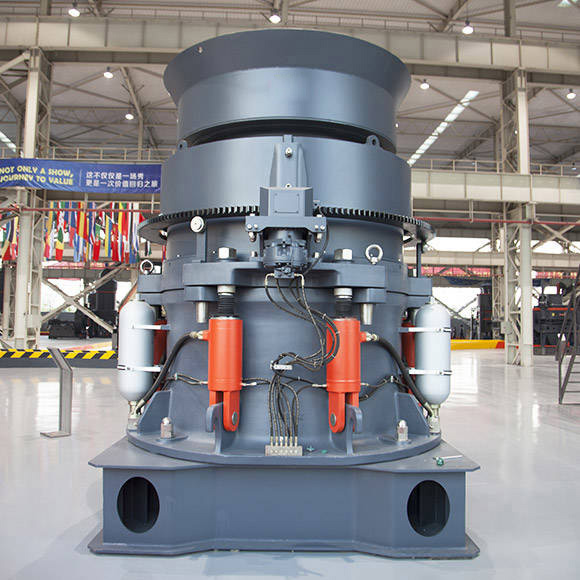
Design Considerations
- Crushing Chamber Design: The heart of a cone crusher is its crushing chamber. Designing a large-capacity chamber involves optimizing the geometry, profile, and liner selection to ensure proper material compression, crushing efficiency, and minimal wear. Computational fluid dynamics (CFD) simulations can be used to refine the chamber design.
- Power and Drive System: To handle larger volumes of material, a high-capacity cone crusher needs a robust power and drive system. It’s crucial to select the right motor, transmission, and drive components to ensure smooth and efficient operation. Variable frequency drives (VFDs) can be used to control the crusher’s speed and power consumption, optimizing energy efficiency.
- Feed and Discharge Arrangement: Efficient material feeding and discharge are critical for maximizing the crusher’s capacity. Properly designed chutes and conveyors can help maintain a consistent feed rate while minimizing spillage and downtime. The discharge system should be designed to ensure uniform material distribution.
- Material Selection and Wear Liners: The choice of materials for the cone crusher components is vital. High-quality, wear-resistant materials for the crushing chamber, concaves, and mantle are essential to minimize downtime and reduce maintenance costs.
- Eccentric and Main Shaft Design: The eccentric and main shaft play a crucial role in the crusher’s performance. Their design should ensure strength, durability, and reliability while minimizing vibration and stress concentrations.
- Automation and Control Systems: Modern cone crushers often include advanced automation systems for process optimization, safety, and remote monitoring. These systems can help operators maximize efficiency, detect issues early, and protect the crusher from damage.
- Safety Features: Safety is paramount in large-capacity cone crusher design. Safety features such as access platforms, guardrails, emergency stops, and automated systems for clearing blockages should be integrated into the design to protect personnel and equipment.
- Maintenance and Accessibility: Easy access to critical components for maintenance is essential. Quick and safe access to the crushing chamber, hydraulics, and other key areas simplifies maintenance procedures, reducing downtime.
- Environmental Considerations: Designing cone crushers with a focus on energy efficiency and environmental impact is increasingly important. This involves using energy-efficient motors, optimizing power usage, and considering emission reduction technologies.
- Testing and Validation: Before a large-capacity cone crusher is put into production, it must undergo rigorous testing and validation to ensure that it meets design specifications and performance requirements. Prototype testing and simulation can help refine the design.
Designing a professional large-capacity cone crusher involves a multidisciplinary approach, considering the engineering, material science, automation, and safety aspects. A well-designed cone crusher can significantly enhance the efficiency of material processing operations in the mining and construction industries, leading to increased productivity and reduced operating costs. Additionally, as technology continues to advance, integrating innovations such as automation and sustainable practices is becoming increasingly crucial in the design process.