A universal jaw crusher is a versatile machine that is extensively used in the mining industry. It is a primary crushing unit suitable for processing various types of materials, including hard and abrasive rocks, gravel, and recycled materials. This type of crusher plays a vital role in the mining sector as it helps in breaking down large rocks into smaller, more manageable sizes, facilitating the subsequent stages of the mining process.
The universal jaw crusher is known for its robust construction and high efficiency. It typically consists of a fixed jaw and a movable jaw that are designed to apply pressure to the material being crushed. The crushing chamber is usually deep and has a large opening, allowing it to process large-sized materials. Additionally, the universal jaw crusher is equipped with heavy-duty components, such as strong and durable bearings, ensuring its reliability and longevity even under demanding mining conditions.
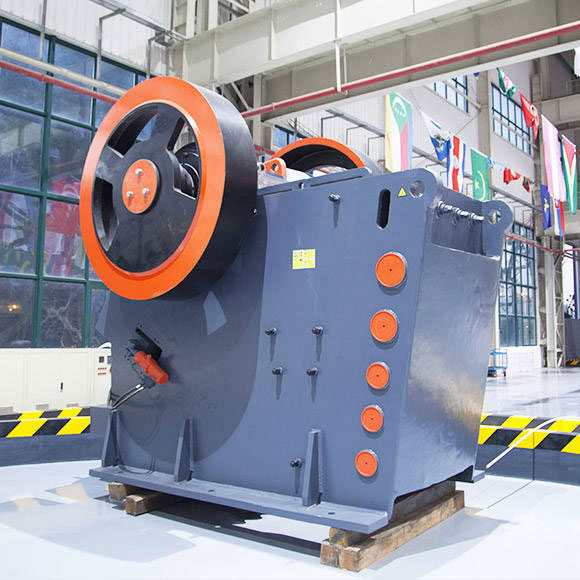
One of the key advantages of the universal jaw crusher is its adaptability to different types of materials. Whether it is hard rock, ores, or industrial minerals, this crusher can effectively handle a wide range of feed materials. Its adjustable settings enable operators to regulate the size of the output material, making it suitable for various downstream processes such as grinding, screening, and conveying. The versatility of the universal jaw crusher makes it an indispensable asset in mining operations.
Furthermore, modern universal jaw crushers are often equipped with advanced features and technologies, enhancing their performance and efficiency. Some models incorporate hydraulic systems that facilitate easy adjustment of the closed-side setting and ensure optimal control over the size of the final product. Others may have automated monitoring systems that provide real-time data on the machine’s performance, allowing operators to make informed decisions and conduct timely maintenance.
In terms of safety, universal jaw crushers are designed with various safety features to protect operators and maintenance personnel. These safety measures include guards, emergency stops, and advanced systems that prevent the crusher from operating when not properly assembled or when there is any potential risk to personnel.
Moreover, the universal jaw crusher is engineered to minimize downtime and reduce maintenance requirements. Components are designed for easy replacement, and regular maintenance routines are straightforward, contributing to increased operational efficiency and reduced overall operational costs for mining companies.
Considering the demanding nature of the mining industry, manufacturers of universal jaw crushers adhere to strict quality standards and continuously innovate to meet the evolving needs of the sector. They prioritize durability, efficiency, and safety to ensure that their machines can withstand the harsh conditions often encountered in mining operations.