A granite processing plant project involves the processing of raw granite stones into various sizes of finished products such as crushed stone, gravel, and sand, which are essential materials in construction and infrastructure projects. This project primarily encompasses the installation and operation of a crusher, which is a crucial component in the granite processing process. With a focus on the crusher, this project will discuss its key aspects and significance within the broader context of a granite processing plant.
The crusher is an essential machine in the granite processing plant as it plays a pivotal role in breaking down the raw granite stones into smaller, manageable sizes suitable for various construction purposes. Typically, a jaw crusher or a gyratory crusher is used for primary crushing, while a cone crusher or an impact crusher may be employed for secondary or tertiary crushing. The specific type of crusher chosen for the project depends on the desired output size and the quality requirements of the final products.
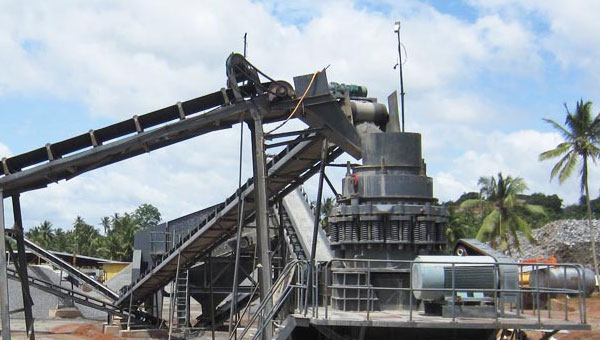
When selecting a crusher for the granite processing plant, several factors must be considered. These include the hardness and abrasiveness of the granite, the required production capacity, the size distribution of the final products, and the initial investment and operational costs. It is crucial to choose a robust and efficient crusher that can withstand the demanding nature of processing hard granite stones while ensuring high productivity and low maintenance requirements.
In the context of the granite processing plant project, the crusher serves as the initial step in the processing chain, enabling the transformation of large granite rocks into smaller, more manageable pieces. The crushed granite materials can then be further processed and refined to meet specific requirements, such as different sizes of aggregates for various construction applications. Moreover, the crusher significantly influences the overall efficiency and productivity of the processing plant, making it a critical component for ensuring smooth operations and timely delivery of high-quality granite products.
Additionally, the installation and operation of the crusher within the granite processing plant project require careful planning and adherence to strict safety and environmental regulations. Adequate measures must be implemented to mitigate any potential risks associated with the operation of the crusher, including dust and noise control, as well as proper waste management practices. Compliance with local regulations and environmental standards is crucial to ensure sustainable and responsible operations throughout the lifespan of the granite processing plant.
Furthermore, incorporating modern technologies and automation systems into the crusher and the overall processing plant can optimize production efficiency, reduce energy consumption, and minimize operational costs. Implementing advanced monitoring and control systems can also enhance the reliability and performance of the crusher, thereby improving overall plant productivity and product quality.