Granite quarries are rich sources of natural stone that is widely used in construction, decoration, and various other applications. The extraction of granite from quarries involves the use of various types of crushers to break down the stone into manageable sizes for further processing. These crushers play a crucial role in the quarrying process, contributing to the production of diverse granite products. Let’s explore some of the common types of crushers used in granite quarries.
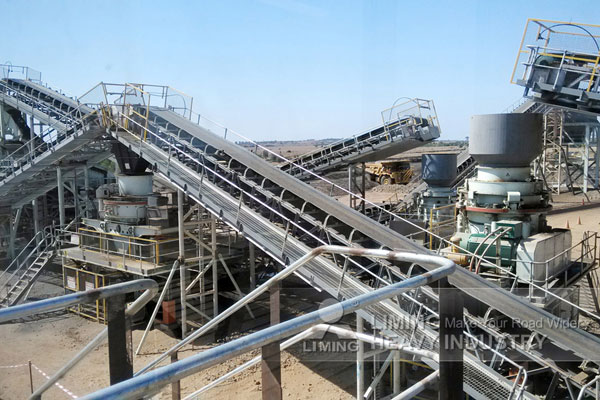
Jaw Crushers:
Jaw crushers are commonly used in granite quarries for primary crushing. These crushers consist of a fixed plate and a movable plate, with the granite rock being compressed between them. The adjustable opening at the bottom allows the crushed material to fall out and continue to be broken until it reaches the desired size. Jaw crushers are known for their efficiency in breaking down hard and abrasive materials, making them suitable for the initial stages of granite processing.
Impact Crushers:
Impact crushers use impact force to break down granite into smaller pieces. They have a high rotational speed rotor with blow bars or hammers that strike the material. This action produces a high amount of fines and is particularly effective for shaping the final product. Impact crushers are versatile and can be used in various stages of crushing, depending on the required size and shape of the granite aggregates.
Cone Crushers:
Cone crushers are utilized in secondary and tertiary crushing stages. They operate by compressing granite between a mantle and a concave. Cone crushers are known for their efficiency in producing well-shaped and finely graded materials. They are often used to produce aggregates for concrete and asphalt production, contributing to the construction industry.
Gyratory Crushers:
Gyratory crushers are similar to cone crushers but have a different shape of crushing chamber. They are typically used in primary crushing and have a higher capacity than jaw crushers. Gyratory crushers are well-suited for handling large pieces of granite. The gyrating motion of the crushing cone within the chamber produces a more uniform product size distribution.
Vertical Shaft Impactors (VSI):
VSI crushers use a different approach by throwing the granite against a spinning rotor with centrifugal force. This action breaks the rock into smaller pieces and shapes them into cubical particles. VSI crushers are particularly effective for producing high-quality sand for concrete and asphalt production.
The types of crushers used in granite quarries are diverse and serve specific purposes in the overall quarrying and processing workflow. Each type of crusher contributes to the production of various sizes and shapes of granite aggregates, which are essential for construction projects, infrastructure development, and other applications. The selection of the appropriate crusher depends on factors such as the size of the granite deposit, desired product specifications, and the overall production requirements of the quarry.