A cone crusher is a powerful machine used in the mining and aggregate industry to crush rocks and reduce their size into smaller, more manageable pieces. It is designed to perform a secondary, tertiary, or quaternary crushing role, depending on the application and the desired end product. In this article, we will explore the key features, working principles, and benefits of cone crushers for rock crushing.
A cone crusher consists of an outer concave, which is fixed, and an inner mantle, which is movable. The crushing chamber is formed by the concave and the mantle. Rocks enter the crushing chamber through the top opening and are progressively crushed as they move down between the mantle and concave. The crushed material exits the bottom of the crusher through a discharge opening.
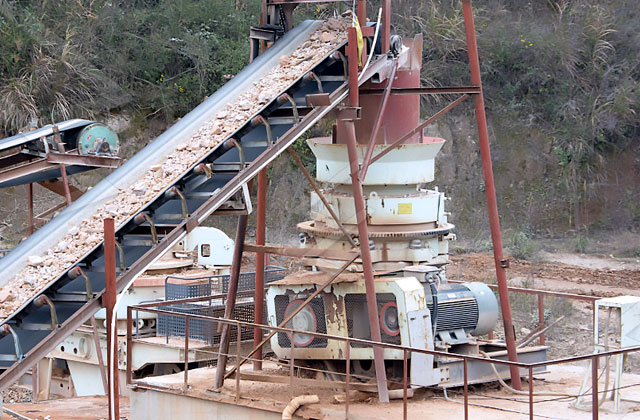
One of the main advantages of cone crushers is their ability to crush hard and abrasive rocks efficiently. They are particularly suitable for processing materials such as granite, basalt, and other similar hard rocks. The design of the crushing chamber ensures that the rocks are subjected to compressive forces between the mantle and concave, resulting in a high reduction ratio and excellent particle shape.
The working principle of a cone crusher is based on the compression principle. As the rocks enter the crushing chamber, they are subjected to a series of compression forces applied by the mantle and concave. The rocks are crushed between the mantle and concave surfaces, which are lined with manganese steel liners for durability. The crushing action is continuous, as the mantle moves in an eccentric motion, creating a gyrating motion that effectively crushes the rocks.
Cone crushers are equipped with a hydraulic system that provides safety and adjustment functions. The hydraulic system allows the operator to adjust the crusher settings to achieve the desired product size and shape. It also provides overload protection, preventing damage to the crusher in case of an excessive load or tramp material.
Another key feature of cone crushers is their versatility. They can be used in various applications and can be easily adapted to different crushing stages. Depending on the required end product, cone crushers can be used as secondary crushers, tertiary crushers, or even quaternary crushers. This flexibility makes them suitable for a wide range of operations, from quarries to mining operations.
In addition to their crushing capabilities, cone crushers offer several other advantages. They have a relatively low operating cost compared to other types of crushers, mainly due to their efficient design and lower power consumption. Furthermore, cone crushers are known for their robustness and durability, allowing them to withstand heavy-duty applications and harsh operating conditions.
Maintenance and servicing of cone crushers are also relatively straightforward. Regular inspections, lubrication, and replacement of wear parts are essential to ensure optimal performance and extend the lifespan of the equipment. Manufacturers often provide detailed maintenance guidelines and offer support and training to operators to ensure proper operation and maintenance.
In conclusion, cone crushers are essential equipment in the rock crushing industry. With their high crushing capacity, efficiency, and versatility, they are widely used in various applications. Whether it is in mining, quarrying, or aggregate production, cone crushers deliver reliable and efficient crushing performance. As technology continues to advance, cone crushers are likely to see further improvements in design and performance, making them even more effective in rock crushing operations.