A barite grinding production line machine is a specialized piece of equipment used in the processing of barite, a mineral that is commonly used in various industrial applications, including oil and gas drilling, chemical production, and paint manufacturing. we will explore the importance of barite, the need for barite grinding production lines, and the key components and processes involved in such production lines.
Introduction to Barite:
Barite, also known as baryte, is a mineral composed primarily of barium sulfate (BaSO4). It is a non-metallic mineral with high density, low solubility, and chemical stability, making it an essential material in various industries. Barite is primarily used as a weighting agent in drilling fluids in the oil and gas industry, where it helps control pressure and prevent blowouts during drilling operations. Additionally, it is utilized in the manufacturing of barium-based chemicals, paints, and coatings.
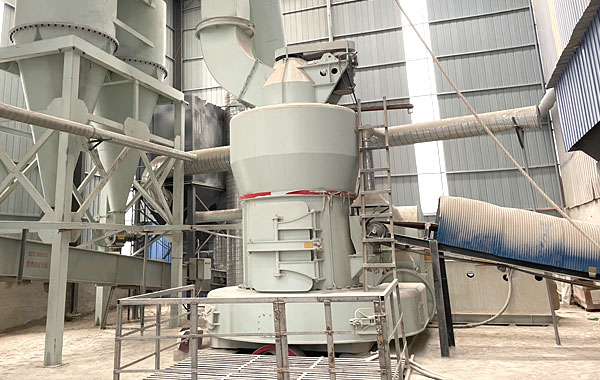
The Need for Barite Grinding Production Lines:
Raw barite ore typically does not meet the specifications required for industrial applications, as it contains impurities and must be processed into a finely ground powder. This process is accomplished through barite grinding production lines, which serve several critical purposes:
- Particle Size Reduction: The primary function of a barite grinding production line is to reduce the size of the raw barite ore to the desired particle size. This is crucial for ensuring uniformity and consistency in the final product.
- Impurity Removal: Barite ore often contains various impurities, such as silica, iron oxides, and other minerals. Grinding production lines are equipped to remove these impurities, resulting in a high-purity barite product.
- Customization: Different industries require barite with specific particle sizes and purity levels. Grinding production lines can be tailored to meet these precise requirements, ensuring that the final product meets industry standards.
Key Components of a Barite Grinding Production Line:
A typical barite grinding production line consists of several essential components:
- Barite Crusher: Raw barite ore is first crushed into smaller pieces by a crusher, which prepares it for the grinding process.
- Barite Grinding Mill: The crushed barite is then fed into a grinding mill, where it undergoes further size reduction. Common types of grinding mills include ball mills, Raymond mills, and vertical roller mills.
- Classifier: To achieve the desired particle size distribution, a classifier is employed to separate the ground barite into different size fractions.
- Dust Collector: The grinding process generates dust, which must be collected to maintain a clean and safe working environment. Dust collectors are used to capture and remove airborne particles.
- Conveyor Systems: Material handling systems, including conveyors and bucket elevators, transport the processed barite between various stages of the production line.
- Packaging and Storage: Once the barite is ground to the desired specifications, it is packaged and stored for shipment to customers.
Barite grinding production line machine is a critical component in the processing of barite, a mineral with widespread industrial applications. These production lines play a crucial role in reducing the size of raw barite ore, removing impurities, and customizing the final product to meet the specific needs of various industries. As the demand for barite continues to grow, efficient grinding production lines will remain essential for ensuring the availability of high-quality barite products in the market.