Mining cone crushers are vital pieces of equipment in the mining industry, utilized for crushing various types of ores and rocks into smaller sizes for further processing. The continuous evolution of technology has led to the development of advanced cone crushers that offer higher efficiency, better performance, and increased safety for operators. Let’s delve into the latest technological advancements in mining cone crushers.
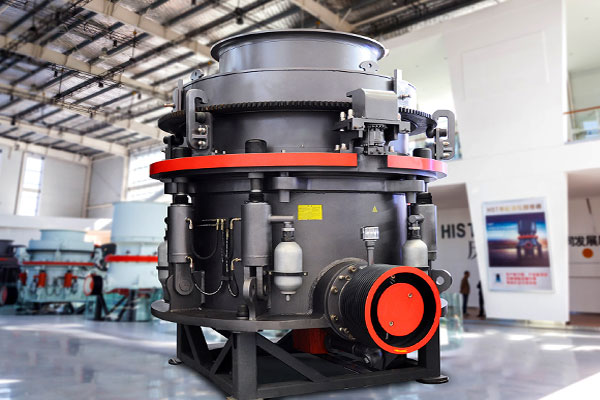
Automation and Remote Monitoring
Modern mining cone crushers are equipped with advanced automation systems that enhance operational efficiency and safety. These systems allow for remote monitoring and control of the crusher, enabling operators to adjust settings, monitor performance parameters, and diagnose issues from a control room or even from remote locations. This not only improves productivity but also reduces the risk to personnel by minimizing the need for physical intervention.
Advanced Crushing Dynamics
The latest cone crushers are designed with advanced crushing dynamics to optimize the crushing process and improve overall efficiency. Features such as adjustable eccentric throw, high pivot point crushing action, and optimized speed and chamber geometry ensure better performance, higher throughput, and improved particle shape, resulting in higher-quality end products.
Improved Energy Efficiency
Energy efficiency is a key focus in the design of modern mining equipment, including cone crushers. Manufacturers are incorporating innovative technologies such as variable speed drives, hybrid power systems, and advanced hydraulic systems to reduce energy consumption during operation. This not only lowers operating costs but also contributes to sustainability efforts by minimizing carbon emissions.
Enhanced Safety Features
Safety is paramount in mining operations, and the latest cone crushers come equipped with a range of features to ensure the safety of operators and maintenance personnel. These include advanced hydraulic systems for overload protection, automatic tramp release mechanisms to prevent damage from uncrushable materials, and improved access for maintenance tasks, reducing the risk of accidents and injuries.
Intelligent Control Systems
Intelligent control systems play a crucial role in optimizing the performance of cone crushers. These systems utilize advanced algorithms and sensor technologies to continuously monitor and adjust crusher settings in real-time based on operating conditions, feed material properties, and desired product specifications. This results in better overall performance, reduced wear and tear, and extended equipment lifespan.
Data Analytics and Predictive Maintenance
The integration of data analytics and predictive maintenance technologies allows mining companies to proactively manage cone crusher maintenance schedules and avoid unexpected downtime. By analyzing operational data and performance trends, predictive maintenance systems can identify potential issues before they escalate into costly failures, enabling timely intervention and maintenance activities to keep the equipment running smoothly.
Material Innovation
Advancements in material science have led to the development of stronger, more durable materials for cone crusher components such as crushing chambers, mantle, and concaves. These materials are engineered to withstand the harsh operating conditions encountered in mining applications, resulting in longer component lifespan and reduced maintenance requirements.
The latest technology in mining cone crushers represents a significant leap forward in terms of efficiency, safety, and performance. With features such as automation, advanced crushing dynamics, energy efficiency, and intelligent control systems, these crushers are poised to revolutionize the way mining companies extract and process valuable minerals. As technology continues to evolve, we can expect further innovations that will drive even greater productivity and sustainability in the mining industry.