A 500 tons/hour limestone crushing production line is a significant industrial undertaking designed to process a large volume of limestone into various sizes of aggregate for use in construction, manufacturing, and other applications. Such a production line typically involves several stages of crushing, screening, and conveying to achieve the desired final product specifications. Let’s delve into the components and processes involved in setting up and operating such a production line.
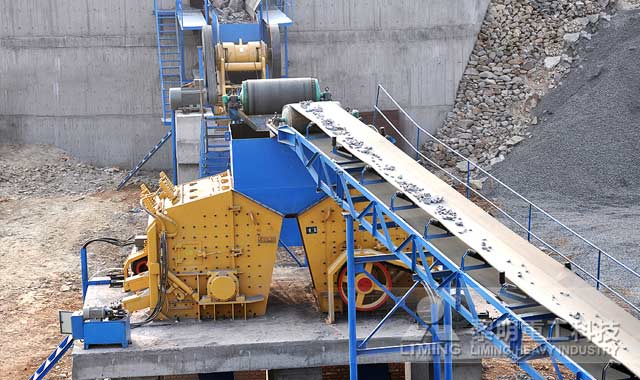
1. Primary Crushing: The limestone extracted from the quarry is first fed into a primary crusher, typically a jaw crusher, where it is reduced in size to a manageable level. The primary crusher’s large feed opening allows for efficient processing of the limestone chunks.
2. Secondary Crushing: After primary crushing, the limestone is conveyed to a secondary crusher, such as a cone crusher or impact crusher, for further reduction in size. This stage is crucial for achieving the desired aggregate size and shape.
3. Screening: Once crushed to the desired size, the limestone undergoes screening to separate it into different grades or sizes of aggregate. This process ensures that the final product meets the specifications required for various applications, such as concrete production or road construction.
4. Conveying: Throughout the production line, conveyors are used to transport the limestone between different stages of crushing and screening. Robust conveyor systems are essential for efficient material handling and to maintain a continuous flow of limestone through the production process.
5. Washing (Optional): Depending on the intended use of the limestone aggregate, a washing stage may be incorporated into the production line to remove impurities and ensure the cleanliness of the final product. This step is particularly important for applications where purity and cleanliness are critical, such as in the production of high-quality concrete.
6. Maintenance and Safety: Regular maintenance of equipment is essential to ensure the smooth operation of the production line and prevent costly downtime. Additionally, strict adherence to safety protocols is paramount to protect workers and maintain a safe working environment.
7. Automation and Control Systems: Modern limestone crushing production lines often incorporate advanced automation and control systems to optimize production efficiency, monitor equipment performance, and ensure consistent product quality. These systems can help operators to maximize throughput while minimizing operating costs and environmental impact.
In conclusion, a 500 tons/hour limestone crushing production line is a complex industrial operation that requires careful planning, efficient equipment selection, and diligent management to ensure its success. By incorporating the right technology, processes, and environmental controls, operators can efficiently produce high-quality limestone aggregate to meet the demands of various construction and manufacturing applications.