Iron ore crushing and screening are integral processes in mining operations that involve extracting iron ore from the Earth’s crust and preparing it for further processing. This crucial stage determines the quality and quantity of the final product, making efficient and reliable equipment essential for maximizing productivity and minimizing downtime. In this essay, we will explore the key components and functions of iron ore crushing and screening equipment.
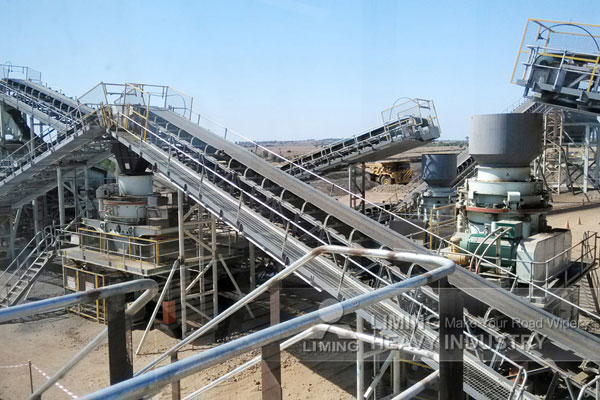
Crushing Equipment:
- Primary Crusher: The primary crusher is the initial stage of the crushing process, where large chunks of raw iron ore are reduced in size to manageable pieces. Typically, jaw crushers or gyratory crushers are employed for primary crushing due to their high capacity and ability to handle large feed sizes efficiently.
- Secondary Crusher: Secondary crushing is often required to further reduce the size of the crushed material for downstream processing. Cone crushers or impact crushers are commonly used as secondary crushers to achieve finer particle sizes.
- Tertiary Crusher: In some operations, a tertiary crusher may be employed to produce even finer iron ore particles. Tertiary crushers, such as vertical shaft impactors, provide the final shaping of the product and are crucial for achieving the desired particle size distribution.
Screening Equipment:
- Scalping Screens: Scalping screens are used to remove oversized materials from the crushed ore stream before further processing. These screens prevent large chunks of ore from entering downstream equipment, thereby improving efficiency and reducing the risk of equipment damage.
- Sizing Screens: Sizing screens are utilized to separate the crushed ore into different size fractions based on particle size. This step is crucial for achieving the desired product specifications and ensuring uniformity in downstream processing.
- Dewatering Screens: Dewatering screens are employed to remove excess moisture from the crushed ore, especially in applications where the ore is being transported or stored in a wet environment. By dewatering the ore, these screens facilitate handling and transportation while reducing the risk of corrosion and degradation.
Key Considerations for Selecting Crushing and Screening Equipment:
- Capacity: The equipment’s capacity must match the production requirements of the mine to ensure uninterrupted operation and optimal productivity.
- Efficiency: High efficiency is crucial for minimizing energy consumption and operational costs. Equipment with advanced features such as adjustable settings and automated controls can improve efficiency and reduce manual intervention.
- Reliability: Reliability is paramount in mining operations, where downtime can result in significant production losses. Choosing robust and reliable equipment from reputable manufacturers is essential for maximizing uptime and minimizing maintenance requirements.
- Safety: Safety is a top priority in mining operations, and equipment must comply with stringent safety standards to protect workers and prevent accidents.
In conclusion, iron ore crushing and screening equipment play a crucial role in the mining process, enabling efficient extraction of iron ore and preparation of high-quality products for downstream processing. By understanding the key components and considerations involved in selecting crushing and screening equipment, mining companies can optimize their operations and achieve greater success in the competitive global market.