The impact crusher is a versatile and widely-used crushing machine that utilizes the principle of impact crushing to reduce the size of various materials. In simple terms, it consists of a rotor, which revolves at high speeds and strikes the incoming material, thereby generating kinetic energy that leads to the fragmentation of the material into smaller particles. This process is highly efficient and effective for crushing a wide range of materials, including rocks, ores, and concrete.
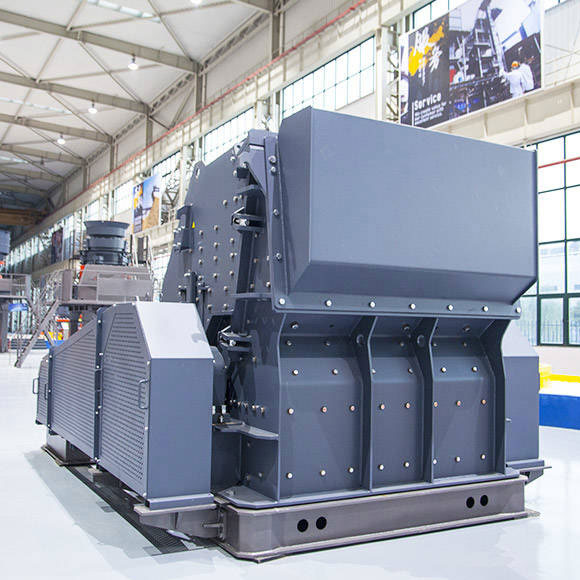
The working principle of an impact crusher can be described as follows:
Feed Material: The raw material is fed into the crusher through a feed chute or hopper. The material enters the rotor, which is equipped with hammers or blow bars that strike the incoming material.
Rotor: The rotor is the main component of the impact crusher and consists of a shaft, discs, and hammers/blow bars. The rotor spins at high speeds, typically ranging from 500 to 3,000 RPM, depending on the desired size reduction ratio and the hardness of the material.
Impact: As the rotor rotates, the hammers/blow bars attached to the rotor strike the material. This impact generates kinetic energy, causing the material to break into smaller pieces. The hammers/blow bars can be fixed or pivoting, depending on the design of the crusher.
Crushing Chamber: The crushed material is then directed to the crushing chamber, which is located beneath the rotor. The crushing chamber consists of an adjustable impact plate and a set of anvils or curtains. The impact plate absorbs the energy from the hammers/blow bars and redirects it towards the anvils or curtains, where further fragmentation occurs.
Size Reduction: The combination of impact forces and the interaction between the material and the crushing chamber result in the size reduction of the material. The size of the final product is determined by the gap between the impact plate and the anvils/curtains, as well as the speed and rotation of the rotor.
Discharge: Once the material reaches the desired size, it exits the crusher through the discharge opening at the bottom of the crushing chamber. The final product can be a well-graded and cubical shape, depending on the settings and configuration of the crusher.
Key features and advantages of impact crushers:
Versatility: Impact crushers can handle a wide range of materials, including soft and medium-hard rocks, ores, and concrete. They are used in various industries, such as mining, construction, and recycling.
High Production Capacity: Impact crushers are capable of producing high volumes of uniform-sized particles. The combination of impact forces and the efficient design of the crushing chamber contribute to their high productivity.
Adjustable Particle Size: The size of the crushed material can be easily adjusted by changing the gap between the impact plate and the anvils/curtains. This allows for the production of different sizes of final products to meet specific requirements.
Energy Efficiency: Impact crushers generally operate at high speeds, which results in efficient crushing with minimal energy consumption per ton of material processed.
In conclusion, the working principle of an impact crusher involves the generation of kinetic energy through the rotation of a rotor and the impact of hammers/blow bars on the incoming material. This process leads to the fragmentation and size reduction of the material, ultimately producing a desired final product. Impact crushers are widely used due to their versatility, high production capacity, and energy efficiency in various industries.