A mineral processing plant is a facility where valuable minerals are extracted from ore through various techniques such as crushing, grinding, and concentration. The grinding mill is a crucial component of the plant, responsible for reducing the size of the ore particles to enable further processing. In this essay, I will discuss the importance of the grinding mill in a mineral processing plant.
The grinding mill plays a fundamental role in the comminution process, which involves the reduction of the ore particle size to a level where valuable minerals can be liberated from the gangue minerals. The primary objective of grinding is to increase the surface area of the ore, allowing for greater contact between the valuable mineral and the reagents used in subsequent processing stages, such as flotation or leaching.
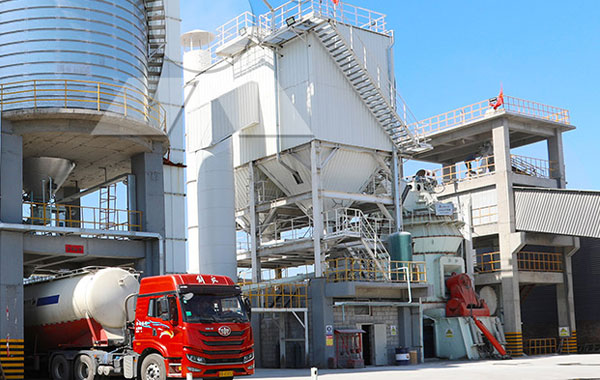
One of the key types of equipment used in grinding is the grinding mill. Grinding mills can be categorized into several types based on the method of grinding they utilize. Some common types include ball mills, rod mills, autogenous (AG) mills, and semi-autogenous (SAG) mills. Each type of mill has its own unique characteristics and is suitable for different types of ores and processing requirements.
The grinding mill consists of a rotating cylindrical shell filled with grinding media such as steel balls or rods. As the mill rotates, the grinding media collide with the ore particles, reducing their size through impact and attrition. The size reduction achieved in the grinding mill is typically in the range of several micrometers to a few millimeters.
Efficient grinding is crucial for the overall performance of the mineral processing plant. The fineness of the ground ore particles directly affects the efficiency of subsequent processing operations. If the ore particles are too coarse, valuable minerals may remain trapped within the gangue minerals, resulting in low recovery rates. On the other hand, if the ore particles are too fine, excessive energy may be consumed in the grinding process, leading to increased operating costs.
The grinding mill also plays a significant role in the liberation of valuable minerals from the ore. In many ores, the valuable minerals are finely disseminated within the ore matrix and are closely associated with the gangue minerals. The grinding mill breaks down the ore particles, exposing the valuable minerals and allowing them to be separated from the gangue minerals in subsequent processing stages. This liberation is often achieved through selective grinding, where different grinding media or operating conditions are employed to target specific minerals.
Furthermore, the grinding mill contributes to the overall sustainability of the mineral processing plant. Energy consumption in grinding represents a significant portion of the plant’s operating costs. Therefore, optimizing the grinding process to minimize energy consumption while maintaining acceptable product fineness is crucial. Modern grinding mills incorporate advanced technologies such as high-pressure grinding rolls (HPGR) and vertical roller mills (VRM), which offer improved energy efficiency compared to traditional grinding mills.
In conclusion, the grinding mill is an essential component of a mineral processing plant. It plays a vital role in reducing the size of ore particles, increasing their surface area, and liberating valuable minerals from the gangue minerals. Efficient grinding is crucial for achieving high recovery rates and minimizing operating costs. Furthermore, advancements in grinding mill technologies contribute to the sustainability of mineral processing operations by reducing energy consumption.