A granite quarry stationary crusher plays a crucial role in the mining and construction industry by facilitating the process of extracting, crushing, and processing granite stone. This stationary crusher, often referred to as a primary crusher, is a key component in the overall operations of a granite quarry. In this essay, we will explore the importance and functions of a granite quarry stationary crusher in detail.
Granite, a durable and aesthetically pleasing natural stone, is widely used in the construction and landscaping sectors. It’s a popular choice for countertops, flooring, monuments, and various architectural elements. However, before granite can be used for these purposes, it must undergo a series of processing stages, starting with extraction from the quarry. This is where the stationary crusher comes into play.
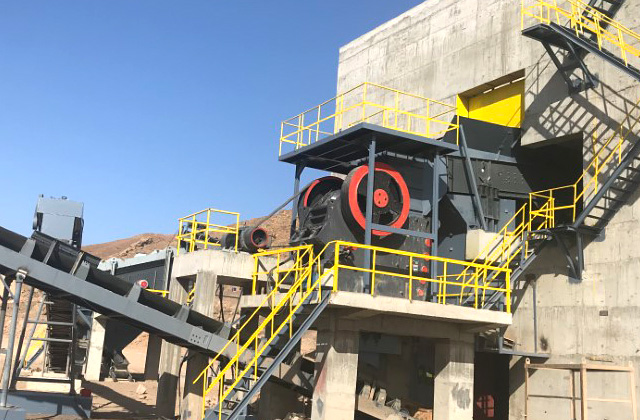
A granite quarry stationary crusher is a fixed machine that is strategically positioned within the quarry site. Its primary purpose is to crush the raw granite extracted from the quarry into smaller, manageable pieces. Let’s explore the key features and functions of these stationary crushers:
Crushing Equipment:
Stationary crushers employ various crushing mechanisms, with jaw crushers and cone crushers being the most common choices for granite processing. Jaw crushers use a swinging motion to crush granite against a fixed surface, while cone crushers utilize a gyrating cone to break down the material. These mechanisms efficiently reduce large granite blocks into smaller sizes.
Product Quality:
The quality of the crushed granite produced by the stationary crusher is crucial. It needs to meet specific size and shape requirements depending on the intended use. High-quality crushed granite is in demand for various applications, including road construction, building foundations, and decorative purposes.
Efficiency:
Stationary crushers are designed for high-capacity production. They can operate continuously, ensuring a steady supply of crushed granite, making them essential for meeting the demands of construction projects that require a steady supply of crushed granite.
Maintenance and Repairs:
Regular maintenance and timely repairs are crucial to keep the stationary crusher in optimal working condition. Downtime can be costly, so preventive maintenance is often scheduled to minimize disruptions.
Environmental Considerations:
To minimize environmental impact, modern stationary crushers are equipped with dust suppression systems to control the release of dust and particulate matter during the crushing process. This helps reduce air pollution and improves the working conditions in the quarry.