The maximum feed particle size of a secondary crusher is a fundamental parameter in the field of mineral processing, mining, and aggregate industries. It plays a pivotal role in the design, operation, and efficiency of crushing circuits. we will explore the importance of the maximum feed particle size, its impact on secondary crushers, and various factors that influence its determination.
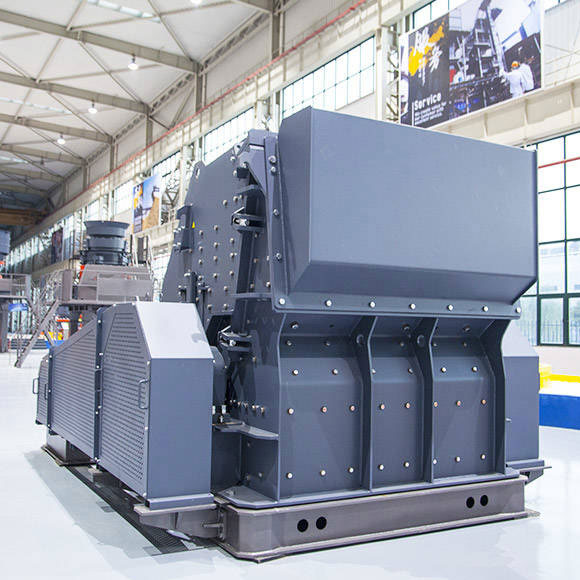
Significance of Maximum Feed Particle Size:
The maximum feed particle size refers to the largest piece of material that can be effectively processed by a secondary crusher. It plays a crucial role in determining the crusher’s capacity, efficiency, and overall performance. Several key factors highlight its significance:
- Crusher Selection: The choice of a secondary crusher depends on the maximum feed size. Different crushers, such as cone crushers, impact crushers, and gyratory crushers, are designed for specific feed size ranges. Selecting the right crusher ensures optimal performance.
- Capacity and Throughput: The maximum feed size directly impacts the crusher’s capacity and throughput. Larger feed sizes typically result in higher production rates, but the crusher must be capable of handling them without excessive wear or downtime.
- Product Size Distribution: The feed particle size affects the product size distribution. For many applications, maintaining a consistent and controlled product size is essential. An oversized feed can lead to coarser output, while an undersized feed may result in finer product.
- Energy Efficiency: Crushing larger particles requires more energy. Therefore, an appropriate maximum feed size helps optimize energy consumption and operating costs.
- Crusher Wear and Maintenance: Excessive large particles can lead to increased wear on crusher components, including the liners and crushing chamber. This can reduce the crusher’s lifespan and increase maintenance requirements.
Factors Influencing Maximum Feed Particle Size:
Several factors influence the determination of the maximum feed size for a secondary crusher:
- Crusher Type: Different types of crushers have varying capabilities regarding maximum feed size. For example, a cone crusher typically accepts larger feed sizes compared to an impact crusher designed for finer crushing.
- Crusher Setting: The crusher’s adjustable settings, such as the closed-side setting (CSS), can impact the maximum feed size. A smaller CSS restricts the feed size, while a larger CSS allows for larger particles to enter the crushing chamber.
- Material Properties: The hardness, abrasiveness, and friability of the material being crushed affect the maximum feed size. Harder and more abrasive materials may require smaller feed sizes to prevent excessive wear.
- Crusher Design: The design features of the crusher, including the size and shape of the crushing chamber, the eccentricity of the mantle or rotor, and the profile of the crushing tools (e.g., concave, mantle, hammers), influence the maximum feed size.