Raymond mill is a commonly used industrial milling equipment, mainly used for barite, calcite, potassium feldspar, talc, marble, limestone, dolomite, fluorite, lime, activated clay, activated carbon, bentonite, kaolin, cement, phosphate ore, gypsum, glass, insulation materials, etc. With the advantages of high grinding efficiency, low energy consumption, high processing capacity, and low noise, Raymond mill has become one of the most important industrial milling equipment in the grinding industry.
The grinding efficiency of Raymond mill is a key factor affecting its quality and output. Improving the grinding efficiency of Raymond mill not only can increase the output of the equipment but also can reduce the energy consumption. There are several methods to improve the production grinding efficiency of Raymond mill:
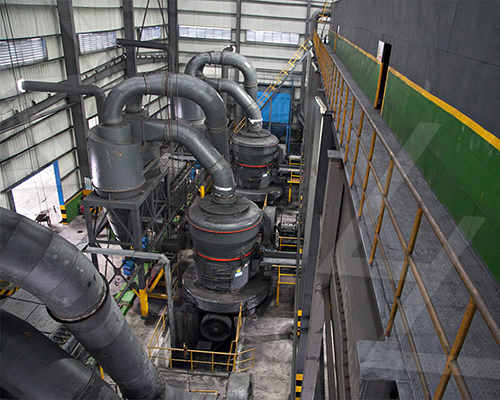
Proper equipment maintenance: Regular inspection and maintenance of the Raymond mill equipment can ensure its stable operation. This includes checking and tightening all parts of the equipment, ensuring the equipment is well-lubricated, and replacing any worn or damaged parts promptly.
Selection of high-quality grinding equipment:
Using high-quality grinding equipment can effectively improve the grinding efficiency of Raymond mill. High-quality grinding equipment is usually equipped with advanced technology and has a longer service life, which can effectively reduce the downtime caused by equipment failure.
Optimize the grinding process parameters:
Adjusting the grinding process parameters, such as the rotation speed of the central shaft, the grinding roller and the grinding ring, the height of the grinding roller, and the size of the grinding ring can effectively improve the grinding efficiency of Raymond mill.
Proper feeding:
Proper feeding is essential to ensure the stable operation of Raymond mill. Uneven feeding or overfeeding may cause blockage or excessive wear of the grinding roller and the grinding ring, thus reducing the grinding efficiency.
Control the humidity of the material:
The humidity of the material has a significant impact on the grinding efficiency of Raymond mill. If the material is too wet, it will easily adhere to the grinding roller and the grinding ring, which will reduce the grinding efficiency and increase the energy consumption.
Selection of suitable grinding aids:
Adding suitable grinding aids can effectively improve the grinding efficiency of Raymond mill and reduce the energy consumption. Commonly used grinding aids include dispersants, grinding aids, and anti-static agents, which can effectively reduce the adhesion between particles and improve the flowability of materials.
Fineness of the finished product:
Proper control of the fineness of the finished product can effectively improve the grinding efficiency of Raymond mill. Controlling the fineness within a reasonable range can reduce the over-grinding phenomenon and improve the grinding efficiency.
By implementing these strategies, the production grinding efficiency of Raymond mill can be effectively improved, leading to higher productivity, lower energy consumption, and better product quality. Regular maintenance, proper operation, and optimization of the grinding process parameters are essential for maximizing the efficiency and performance of Raymond mill.