A vertical roller mill is a type of industrial equipment used to crush or grind materials into small particles. It’s widely used in the concrete and mining fields, and more recently in the recycling industry. The design of a vertical roller mill allows it to dry, grind, and classify all within one piece of equipment, making it an efficient and versatile piece of machinery for various industries.
One of the critical aspects in the operation of a vertical roller mill is the control over the particle size distribution of the ground material. The particle size directly influences the properties of the final product and impacts various parameters such as the product’s performance, handling characteristics, and market value. Therefore, optimizing the particle size distribution is crucial for achieving the desired product quality and ensuring efficient processing.
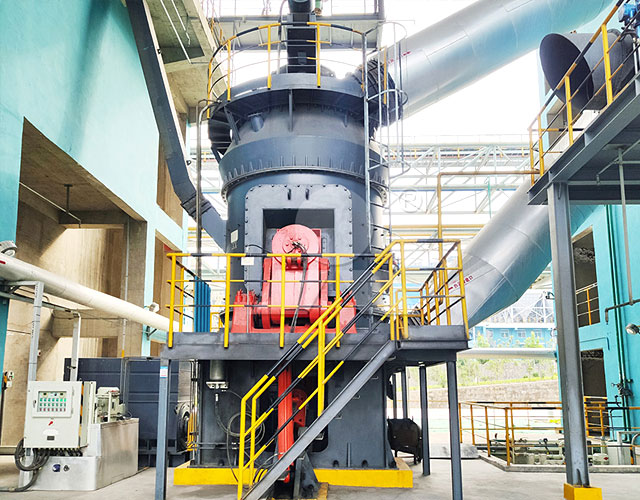
The production particle size in a vertical roller mill is typically controlled through several factors, including but not limited to:
- Mill Configuration and Design: The design of the mill, including the number and size of rollers, their speed, and the table configuration, can have a significant impact on the final particle size distribution. Adjustments to these parameters can help achieve the desired particle size range.
- Feed Rate and Material Properties: Controlling the feed rate of the material being processed and understanding its physical and chemical properties is essential. Different materials have different grindability and behavior under grinding, so adjusting the feed rate can help achieve the desired particle size distribution.
- Grinding Pressure and Classifier Speed: The grinding pressure and classifier speed are two crucial parameters that influence the particle size distribution. Adjusting these parameters can affect the residence time of the material inside the mill and consequently impact the final particle size distribution.
- Separation Efficiency of the Classifier: The efficiency of the classifier in separating the fine and coarse particles can greatly affect the particle size distribution. A well-functioning classifier ensures that the desired particle size range is achieved consistently.
- Material Moisture Content: The moisture content of the material being processed can affect the grinding process and the final particle size distribution. Ensuring optimal moisture content can help achieve the desired particle size and prevent issues such as clogging and inefficient grinding.
To achieve a specific particle size distribution in the production of a vertical roller mill, it is essential to closely monitor and adjust these parameters as needed. Process control systems and advanced technologies can be employed to automate and optimize the milling process, leading to improved efficiency and consistent product quality.
Furthermore, the use of advanced modeling and simulation techniques can aid in predicting the particle size distribution based on various operating parameters, thereby assisting in the optimization of the milling process for specific materials and end-product requirements.