A secondary rock crusher plays a crucial role in the mining process by reducing the size of ore particles that have been extracted from the primary crusher. This type of crusher is essential in the ore processing chain, as it ensures that the ore is finely crushed to facilitate further processing, such as milling and separation. The dimensions of a secondary rock crusher are a key consideration in its design and performance, impacting factors like throughput, efficiency, and maintenance.
The primary function of a secondary rock crusher is to take coarse ore from the primary crusher and further reduce it to a size that can be easily handled by downstream equipment. Typically, secondary crushers are cone crushers or impact crushers, each with its advantages and limitations. The choice between these types depends on the specific requirements of the mining operation.
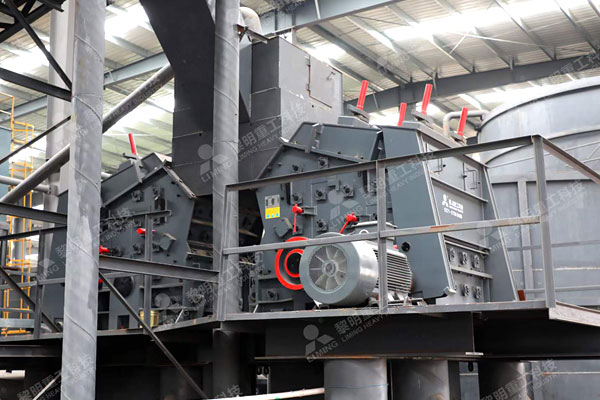
Dimensions and Throughput:
The dimensions of a secondary rock crusher are critical in determining its throughput capacity. Throughput refers to the amount of material that can be processed within a given time frame. This parameter is influenced by the size of the crusher’s opening, commonly referred to as the feed opening, and the chamber geometry. A larger feed opening allows for larger chunks of ore to enter the crusher, while the chamber geometry affects the crushing process and the product size distribution.
Feed Opening:
The size of the feed opening is a key factor in the crusher’s ability to handle different sizes of ore. A wider feed opening accommodates larger rocks, reducing the need for pre-screening and ensuring a more efficient crushing process. However, the trade-off is often seen in increased power consumption and wear rates.
Chamber Geometry:
The design of the crushing chamber influences the crusher’s performance. Different chamber geometries result in varying compression ratios and product shapes. A well-designed chamber promotes efficient crushing, ensuring that the energy input is utilized effectively. Additionally, it contributes to the production of a well-graded and cubical product, which is essential for downstream processes like milling.
Efficiency and Power Consumption:
Efficiency is a critical aspect of secondary rock crushers. It is influenced by factors such as the crusher’s design, chamber geometry, and the type of crushing mechanism. Modern crushers often feature advanced technologies, such as hydraulic systems and electronic control units, to optimize performance and minimize energy consumption.
Maintenance Considerations:
The dimensions of a secondary rock crusher also affect maintenance requirements. Access to key components, such as the crushing chamber and wear parts, should be considered during the design phase to facilitate routine maintenance and repairs. This is essential for minimizing downtime and ensuring the continuous operation of the mining process.
In conclusion, the dimensions of a secondary rock crusher are integral to its overall performance and efficiency in the mining process. Engineers and designers must carefully consider factors such as feed opening size, chamber geometry, and ease of maintenance to optimize the crusher for the specific requirements of the mining operation. A well-designed and properly sized secondary rock crusher contributes to the overall success of the ore processing chain, ensuring the production of high-quality material for further downstream processes.