A river pebble production line with a cone crusher as its central equipment is a sophisticated system designed to process river pebbles into various sizes of aggregates for construction and landscaping purposes. This production line involves several key components and processes aimed at efficiently crushing, screening, and shaping river pebbles to meet specific requirements. Let’s delve into the details of how such a production line operates.
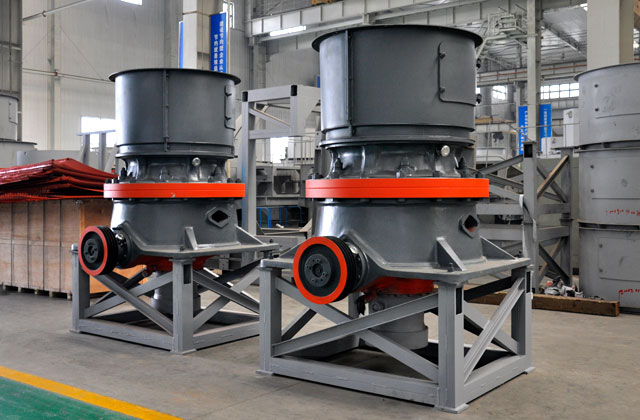
Primary Crushing: The primary crushing stage involves feeding the raw river pebbles into a cone crusher. Cone crushers are commonly used in river pebble production lines due to their ability to crush hard and abrasive materials efficiently. Within the cone crusher, the river pebbles are subjected to high compression forces as they are squeezed between the mantle and concave liners. This action breaks the pebbles into smaller fragments of the desired size range.
Screening and Classification: Following the primary crushing stage, the crushed river pebbles pass through a series of vibrating screens. These screens are equipped with different-sized openings, allowing the aggregates to be sorted into various size fractions. Oversized pebbles are returned to the cone crusher for further crushing, while properly sized aggregates proceed to the next stage of processing.
Secondary and Tertiary Crushing (Optional): Depending on the desired final product specifications, secondary and tertiary crushing stages may be incorporated into the production line. Secondary crushers, such as impact crushers or vertical shaft impactors (VSI), can further reduce the size of the river pebble aggregates. Tertiary crushers may be employed to produce even finer materials if necessary.
Shaping and Sand Making: River pebbles often undergo shaping and sand making processes to enhance their aesthetic appeal and usability in construction projects. This may involve passing the crushed aggregates through a vertical shaft impact crusher (VSI) or a sand making machine. These machines use high-speed rotors to impart kinetic energy to the river pebbles, shaping them into cubical or rounded forms and producing sand with desired gradations.
Washing and Final Processing: To ensure the cleanliness and quality of the final product, washed aggregates may undergo additional washing processes. This step removes any remaining impurities or fine particles adhering to the surface of the river pebbles. After washing, the aggregates are conveyed to storage bins or stockpiles for distribution or further processing.
Quality Control and Testing: Throughout the production process, quality control measures are implemented to monitor the size distribution, shape, and cleanliness of the aggregates. Samples are regularly collected and tested in laboratory settings to verify compliance with applicable standards and specifications.
Furthermore, the modular design of cone crusher systems facilitates easy integration into existing river pebble production lines or the establishment of new facilities with minimal lead time. Manufacturers offer a range of customizable configurations, allowing operators to tailor the crushing equipment according to specific production requirements and site conditions. This adaptability ensures optimal performance and longevity of the production line, contributing to long-term cost savings and operational efficiency.