Cement grinding is the final process of cement manufacturing. Its main function is to grind cement clinker (and retarder, performance adjusting material, etc.) to a suitable particle size (represented by fineness, specific surface area, etc.) to form certain particles. Gradation, increase its hydration area, accelerate the hydration rate, and meet the requirements of cement paste coagulation and hardening.
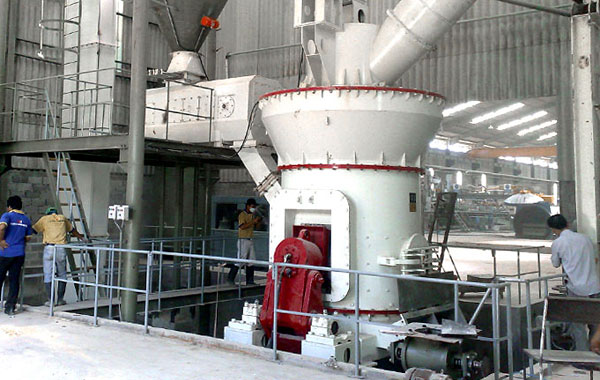
The production process of cement
- The cement raw materials are firstly crushed by the crushing process. The crushed cement materials are sent to the silo by the elevator, and then sent to the grinding chamber of the mill evenly and quantitatively by the vibrating feeder for grinding.
- The ground material is classified by the powder separator, and the unqualified powder is classified by the powder separator and then returned to the main machine for re-grinding.
- The cement powder that meets the fineness enters the dust collector through the pipeline with the airflow for separation and collection, and the collected finished cement powder is sent to the finished product silo by the conveying device through the discharge port, and then unified with the powder filling tanker or automatic baler.
Grinding equipment for cement production
The grinding equipment used for cement production mainly includes: vertical mill, ball mill, European mill, trapezoid mill and Raymond mill.
Cement production vertical mill
The vertical mill for cement production is mainly composed of a separator, a grinding roller device, a grinding disc device, a pressurizing device, a reducer, a motor, and a shell. The separator is a high-efficiency and energy-saving powder sorting device. The grinding roller is the part used to grind and pulverize the material. The grinding disc is fixed on the output shaft of the reducer, which is the place where the grinding roller rolls the material. The pressure device is The part that provides the grinding force to the grinding roller, providing enough pressure to the grinding roller to crush the material.