The jaw crusher has been developed and designed in combination with customer needs and market conditions, and has greatly improved in terms of motion parameters, structural forms, and adjustment methods, and the depth of the crushing cavity has increased the throughput. It uses oversized bearings and forged spindles to carry crushing loads. Greater force, coupled with flywheel design, can effectively reduce vibration and run more smoothly, with an output of 1-1160 tons per hour.
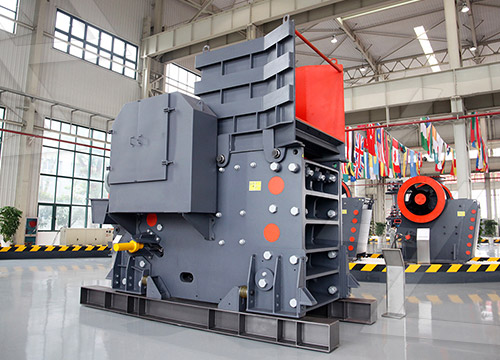
Application of jaw crusher
The jaw crusher is curved extrusion crushing, and the motion parameters are optimized at the same time, so that the material can start to be crushed at the upper part of the crushing cavity, and the stroke at the lower part of the crushing cavity is larger, the crushing ratio is larger, and one machine is multi-purpose. It is widely used in mining, smelting, Building materials, highways, railways, water conservancy and chemical industries.
The working principle of jaw crusher
The jaw crusher uses wedges to adjust the discharge opening, which is easier to adjust and has a large range, usually around 10-350mm, which can meet the requirements of different users. Block content, stone powder content, crushing index, harmful substances, bulk density, porosity, etc. meet the use standards.
Material processing of jaw crusher
The jaw crusher is mainly used for crushing various ores and rocks with a compressive strength of 147-245MPa. For this kind of high hardness stone, the key components such as jaw plate and lining plate are all made of high-quality alloy materials. The machine is durable, as well as granite, basalt, limestone, quartz stone, coal gangue, construction waste, etc.